Food waste separators for depackaging and contaminant material removal from all types of inedible food are in increasing demand.
A major challenge faced at food waste processing plants by plant operators is to remove all plastics and packaging leaving pure organic content that is used via anaerobic digestion to produce biogas as well as sell renewable energy.
Rising Need for Food Waste Separators
New targets have been set in the US, at state level, to raise the level of food waste biogas production which will bring huge benefits in the fight against climate change. Many other nations are also striving for food waste reduction in a similar way.
This includes the largest nations throughout the EU and globally. And, in the US some states have started their own Food2Energy programs and have plans to limit or eventually ban the disposal of organic waste to their landfills.
This means that the number of food waste digestion facilities are about to grow rapidly – and every one of them will need highly efficient materials separation and depackaging.
This will result in the diversion of the most damaging remaining type of waste currently still allowed to be deposited in a sanitary landfill, away from them to AD plants. In these plants, the enormous amount of energy the food waste contains will become much-needed renewable fuel, not least as biomethane to fuel transport vehicles. It is already seeing a rapid take-up to power heavy goods vehicle engines.
But that won’t save the planet alone. Solving the plastics contamination problem must also be achieved to prevent an ever-rising tide of plastics clogging up the oceans and destroying marine life.
However, don’t despair because technology is improving rapidly. Read on to find out how and why that is happening!

Why Food Waste Separator and Depackaging Technology is Important
The challenge for the food waste processor plant operators, who overwhelmingly use the anaerobic digestion process to produce biogas and sell renewable energy output they create, is to remove everything bar the organic content.
The escape of plastics in all forms into the environment is now recognised for the scourge it truly is. No matter how well food waste AD plants extract the energy from unwanted food those plants will not be sustainable if they allow the output of plastics into the environment.
Within geological timescales mountain ranges erode and all plastic will be washed into the oceans. And, yet if removed the plastic often can be recycled and reduce the need for extracting more climate change inducing fossil fuels from the ground.
Almost all packaging is a contaminant, including the ASTM-compliant biodegradable polymers that may soon become more commonly used. The squeezable package pouch housing a juice drink, the expanded polystyrene foam used to construct a compact sandwich tray, and the omnipresent film plastic used to cover and carry it all are all examples of packaging.
The development and wholesale adoption of effective food waste separation methods including depackaging technology could not be more important. It is vital to a sustainable planet.
Recent Developments in Separation and Depackaging Technology
The leading waste processing companies have been quick to recognize that demand is rising for the efficient removal of all packaging and other unwanted materials from food waste.
Since the early hammermill-based or centrifuge-based devices, (and with most requiring a bag opener or shredder), food waste depackagers have come a long way.
These methods are used by wet digestion facilities that handle commingled source-separated food wastes from commercial and/or residential diversion programmes to reduce all sorts of troublesome material entering their digestion reactors.
But new market opportunities are also being generated by this equipment. Machines that cut apart and separate packaging, such as tubs of cream, cereal boxes, plastic bags of frozen prawns, and shrink-wrapped meat and vegetables, are increasingly being installed.
Food Waste Separators – Game-Changing Technology
This game-changing technology is now opening new recycling opportunities for packed organic materials, as well as the packaging in some situations.
But until now, depackaging equipment is costly, ranging from $250,000 to $500,000 for the separator alone. On top of that, a few hundred thousand dollars will be required for auxiliary infrastructure works, such as a building, receiving area, and liquid storage tanks.
There has been a need for equipment that will perform multiple functions in one device, saving not only on capital cost but also on the cost of supervisory staff and valuable space.
One of those functions must also be the removal of grit, sand and silt which is capable of building up to ultimately render biodigesters which require a total opening up and physical cleaning out.
That’s where the new Twister Universal Depackager and Separator with Seditank technology, recently brought to our attention by Mark Vanderbeken Chairman and Founder of Drycake, has many strengths.
The Twister Universal Depackager with Seditank
The Twister De-packager and Separator is based on DRYCAKE's 25-year separation technology experience and is their 3rd generation of VERTICAL CYCLONIC SEPARATOR technology. It allows users to efficiently separate packaging from food or other organic material and performs multiple functions in one compact unit.
The Twister is justifiably described as the most adaptable food waste unpacking solution on the market. It unpacks and isolates contamination from food waste so that it can be processed for anaerobic digestion and composting facilities.
The Twister can be fed with a front loader or overhead crane, as well as a belt conveyor or other custom-made system at existing installations. In new installations, the Twister can be fed automatically from the bunker without the need for an operator or moving equipment.
An upper screw is provided in the hopper to prevent bridging, while the lower screw feeds the Twister separator. It includes a patented bag opener inside.
A Twister style vortex created inside the screening drum forces the organics through the perforations while the paddles interact with the packaging on its way upward in the Twister movement. This allows impurities to escape through the tangential exit. The result is a completely clean soup ready to feed into the digester tank and dry and clean packaging placed in a skip ready to recycle.
Their Seditank unit comes as part of the package and removes microplastics, silt, sand, and grit while adding water.
The process represents a practical rethink of the traditional separation technologies used in the waste industry and is well worth consideration by anyone looking for next-generation separation of food waste.
Upstream Depackaging and Separation Vs Downstream Removal
Surprisingly, until now the separation and depackaging stage has in the past often been left until last. Until after the digestion stage.
That means that the digestate is free from plastics and other foreign materials only after the process. While this is certainly is needed it is far better to separate and depackage first.
The digestate can usually only be used as a fertilizer spread on land after a high degree of separation and depackaging, but the latest systems will remove the contamination upstream of the anaerobic digestion stage, which is far better.
In reality, the degree to which food waste AD processors achieve depackaging and separation, before entering the process tanks, is a no-brainer. The key factor for successful long term digester operation is to do so without shut-downs to remove the build-up of plastics, grit and other unwanted items. This is crucial for all operators.
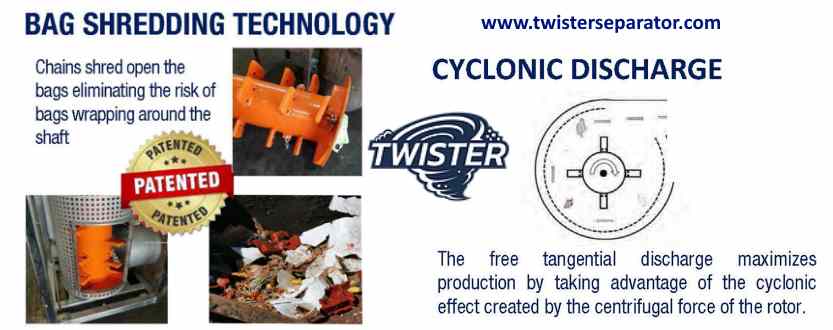
Why Digester Shut-Down for Grit and Accumulated Plastic Removal Must be Avoided
For any biogas plant operator to have to drain, empty and clean their biodigester is a nightmare. The costs due to lost production are bad enough, but the accumulated sludge may need to be disposed of as hazardous waste at an additional huge cost.
This is without even mentioning the loss of client goodwill if waste food deliveries must be curtailed over a period of months while an anaerobic digestion tank is biologically recommissioned.
The best models separate packaging with only as much force necessary and avoid the packaging splintering. Depackager options are described below.
Use of Food Waste Separators at Composting Plants
It is worth mentioning here that some of these devices may be well worth the investment for composting facilities that handle similar wastes. They can cut contamination removal costs, reducing the need for final shredding and small sieve-sizings to catch plastic particles and open up new tipping (gate-fee) revenue prospects for industrial food product depackaging and recycling to composting companies. While at the same time we accept that many organisations will seek the more sustainable option of AD plant processing.
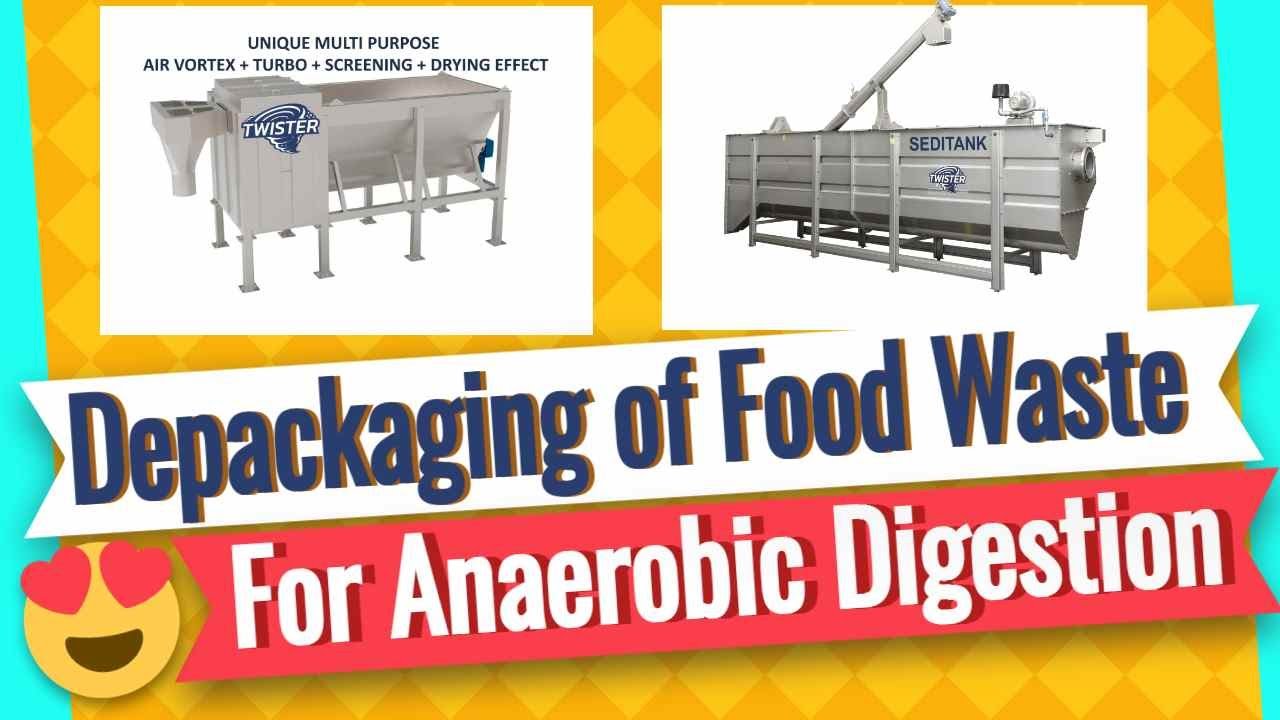
What Food Waste Separation with Depackaging Can Mean for Food Waste Producers
A few food waste producers depackage their own waste food. But most don’t even try, right across the wide-ranging scope of pre-consumer, packaged food waste in all forms. That includes post-consumer, mixed source separated organics (SSO) from such as restaurants, supermarkets, sports attractions, colleges, etc.
Yet, properly source-separated organic wastes can gain real value when a synergistic partner organisation can be found which can utilise specific food wastes of known origin and quality.
For these waste producers, they may be sitting on an asset within the emerging circular economy.
For these businesses, the latest food waste depackaging equipment opens up a new possibility of, automated in-house separation, for food waste producers who wish to reduce their food waste disposal costs. At the same time, they will be able to report significant gains in company sustainability.
In nations such as Scotland where organic waste landfill bans are proposed depackaging and separation may be the only viable option available. That’s because the packaging must be removed for AD plant processing or composting.
The Scottish Government's Climate Change Plan update outlines plans to stop all non-household biodegradable trash from entering landfills by 2025. The plans are part of a set of policies aimed at reducing food waste by a third by 2025 and recycling 70% of total garbage.
Even when as much food as possible is recovered for food banks and animal feed, there still remains off-spec packaged food that originates from:
- out-of-date,
- spoilt,
- mislabelled, and
- damaged products,
and this can account for a large amount of a manufacturer's waste volume.
If so, companies will do well to seek out the latest equipment we have described here.
Conclusion: The End of Manual Source Separation of Food Waste?
Food comes in an almost unlimited range of materials, forms, weights, and densities when it comes to packaging making and as a result, its separation requires truly innovative technology.
Regardless of how well-trained workers are in source separation of food wastes, the purity of source-separated organics (SSO) will always be less than 100%, and in some cases, significantly less.
However, the trend is for new technology in food waste depackaging and separation is that this technology may soon replace all manual separation labour.
The need for food waste separators to:
- keep contaminants and especially plastics out of feedstocks for wet anaerobic digester systems and the compost-based end product(s),
- as well as cut the costs and difficulties of doing so using human labour,
- plus, expand repackaging capacity to cope with the rapid and rising uptake of the anaerobic digestion process as the prime method for treatment and disposal of all food wastes when all else fails and only energy recovery remains as an option,
has led to the development of innovative technology that can separate and repackage food waste reliably.
[First posted in 2021.]
What is the total number of installations you have across the world? Thanks’
In excess of 20,000 certainly (my own opinion). Most are home or homestead type plants in China, and India.
Even something as basic as food has been screwed up by humans, and it’s mind-boggling!