Selecting anaerobic digester mixing systems to obtain the lowest cost of ownership is important for any biogas plant operator. To consistently produce a high rate of biogas production, anaerobic digesters rely on efficient mixing systems to break up scum and solids and distribute them throughout the digester.
The cost of purchasing, operating, and maintaining these mixing systems, on the other hand, can be a significant barrier to adoption.
To make anaerobic digestion financially viable, it is critical to select a mixing system with the lowest total cost of ownership over its lifetime.
In this article, we'll look at the key factors to consider when selecting the most cost-effective anaerobic digester mixing systems for efficient and sustainable biogas production. We will follow that with a real-life case study provided by a recent Landia Press Release.
How to Select an Anaerobic Digester Mixing System for the Lowest Cost of Ownership
The term “Lowest Cost of Ownership” refers to the total cost of owning and operating a specific asset over its entire life cycle. It considers not only the purchase price but also ongoing expenses such as maintenance, repair, and operating costs.
In the context of anaerobic digester mixing systems, the lowest cost of ownership means selecting a system with a low initial cost as well as low ongoing expenses over the system's life. This ensures that the system will provide a good return on investment and will be financially viable in the long run.

Factors to Consider when Selecting Anaerobic Digester Mixing Systems
To achieve the lowest cost of ownership, consider the following factors when selecting anaerobic digester mixing systems:
- Efficiency of mixing: The mixing system must be effective at breaking up scum and solids and distributing them throughout the digester. This promotes efficient biogas production while reducing the need for manual intervention.
- Energy consumption: The mixing system should consume little energy, as energy costs can add up quickly over the system's lifetime. Look for a system that has a low overall power requirement and uses energy-efficient components.
- Maintenance needs: The mixing system should be easy to maintain and repair, with readily available replacement parts. This helps to cut down on downtime and repair costs.
- Durability and lifespan: The mixing system should be built to last and be able to withstand the harsh conditions found inside a digester. A longer lifespan reduces the need for replacement and the costs associated with it.
- Compatibility: The mixing system must be compatible with the type of digester and materials being processed. This ensures that the system operates at peak efficiency while reducing the risk of damage.
By taking these factors into account, you can select an anaerobic digester mixing system with the lowest cost of ownership, thereby ensuring long-term financial viability and success.
Press Release 15 February 2023:
Biogas benefits at the farm with tough new mixers

A farm in Kent's northwestern corner has improved its biogas operation significantly by upgrading the mixing system for its two 4500m3 anaerobic digesters.
Oncoland Farm (part of The Billings Group) was having issues with the mixers installed when the gas-to-grid AD plant was built in 2020 as part of its ongoing diversification.
Historically a mixed farm of arable, dairy, and beef, Oncoland has successfully added hops, vines, and renewable energy to its portfolio as part of its Net Zero initiative.
However, as Plant Manager Carl Woolley discovered, the mixers included in the package deal were unsuitable for the feedstock, which combines the farm's cattle slurry with waste from the 2500-acre site's vegetables, such as cabbage, potatoes, and carrots.
Oncoland's feedstock also includes waste pomegranate and mango, which go through a hammer mill first.
“The originally supplied anaerobic digester mixing systems would have probably been fine for a standard mix or maize and slurry,”
said Carl,
“but for a plant such as ours with varying types of waste, you need much sturdier equipment. Only six months into us producing biogas, we started to see that the submersible mixers were beginning to fail due to the ingress of water. Although the separate, paddle mixers in the digesters continued to do their job, over time, the submersible mixers, one by one, gave up the ghost”.
Working closely with James Gorridge at Mid-Kent Electrical Engineering (MKE), Carl looked at how best to resolve the issue with the submersible mixers and get the plant to its optimum operation.
“We weighed up the costs of retrieving the faulty mixers for repair and rewinding,”
said James Gorridge,
“but we both knew how disruptive that would be to the whole process, and the fact that we’d be fixing equipment that was inevitably going to fail again in only a short period of time”.
“More cost-effective and reliable in the long term’”.
Carl Woolley added:
“Removing the submersible mixers would have first involved waiting for dry, calm weather and hiring a crane. Then, two full days of arduous work and a huge amount of downtime halting the biogas process, emptying the digesters and starting everything up again.
We both went away to consider the best, long-term solution. MKE has always supplied us with very good quality motors and drives, with a very good turnaround and attention to detail, so I knew they believed in quality.
During my career, I’d seen just how robust mixers and pumps are from Landia. And based on his separate previous experience with Landia equipment, James agreed that despite the higher capital investment, their mixers would actually work out to be far more cost-effective and reliable in the long term, significantly reducing our maintenance costs”.
When the four failing submersible mixers were finally removed, it was discovered that their propellers had actually experienced very little wear.
“This was because they were the wrong shape and didn’t really do anything”,
continued Carl Woolley.
“With just a couple of basic seals, they just weren’t designed for this type of biogas application, so had started to let liquid in very early after they were installed”.
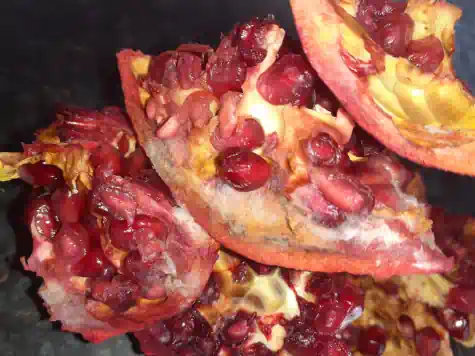
To optimise the process, Carl and MKE also saw that the anaerobic digester mixing systems had been underspecified, so chose to go up a mixer size.
“We knew this would further improve the mixing, which is crucial for any biogas plant”,
added James Gorridge from MKE.
“It would also have less impact on the new mixers from Landia, which would only have to run for 20 minutes per hour (compared to 24/7 for the failed mixers), saving considerably on energy consumption”.
Four of Landia’s POP-I (18.5kW 300rpm) mixers were installed (two on each digester), with an immediate positive effect on the process, which typically handles dry solids of around 8% and higher.
‘Comprehensive mixing’
“Previously”,
said Carl Woolley,
“it took time for everything in the tanks to get going, but the new Landia mixers resuspended the contents almost immediately. We now get comprehensive mixing and no crust whatsoever. The other important benefit is that the mixers are easy to maintain, especially with their twin-mechanical seals.”
In addition to the two primary digesters, Oncoland’s pre-treatment tank (70m3) has also benefitted from an upgrade to more suitable equipment; this time with a Landia Chopper Pump (invented by the company in 1950).
‘Constantly conditioned’
“We took the opportunity to widen our upgrade to the pre-treatment tank,”
said Carl Woolley.
“Again, the submersible mixer that was supplied as part of the plant package wasn’t up to the job, leaving lumps in the feedstock and dead spots in the tank. But now with the Landia Chopper Pump (11kW), which is extremely reliable, the feedstock of slurry from our dairy unit, plus the vegetable and fruit waste, is constantly conditioned so that our process benefits from a consistent soup. The Chopper Pump’s blades remain fine and sharp”.
He added his thoughts on the new Landia anaerobic digester mixing systems:
“With both the Landia pump and mixers, we now have peace of mind. Working with James at MKE, we saw that we could have bought mixers at around £4K less per unit, but biogas feedstocks are unforgiving. The whole process is about learning and nurturing. There’s just no hiding place for equipment that isn’t sturdy. We bought on reputation and can see already what a sound investment it has been.”
“Biogas is a different beast in the UK, so best buy the mixers and pumps that are fit for purpose.”
www.landiaworld.com | www.mke.co.uk
Concluding This Article on Anaerobic Digester Mixing Systems
In conclusion, for efficient and long-term biogas generation, the mixing system for the anaerobic digester should have a low total cost of ownership.
Anaerobic digestion plant operators can optimise their return on investment and secure their company's long-term financial health by carefully considering a number of parameters, including:
- mixing efficiency,
- energy consumption,
- maintenance needs,
- durability and longevity,
- while never forgetting compatibility.
Reducing the total cost of ownership for an anaerobic digestion system has the potential to increase its adoption and use as a waste-to-energy conversion technology, hence bolstering the expansion of the renewable energy market.
More sustainable futures and less reliance on nonrenewable energy sources are possible with the adoption of cutting-edge technologies such as those provided by Landia and their best practices in anaerobic digester mixing systems.
Would it be possible to create a hybrid digestor that can switch between mesophilic and thermophilic digestion? So is there no way to choose between the two options other than to pick either one?