Once again digester mixers installed by Landia have turned out to be a crucial component for success when taming a troublesome AD facility.
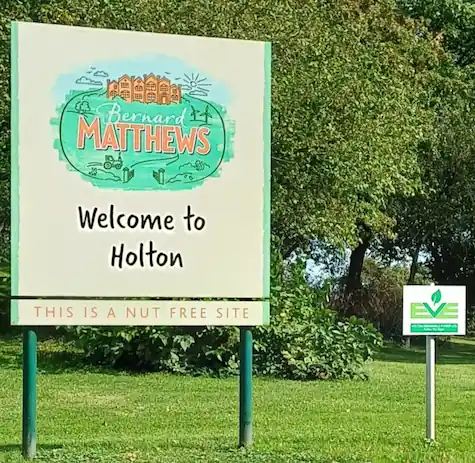
Let's have a natter about a proper success story. I'm talking about Eco Verde Energy's (EVE) revamp at their Anaerobic Digestion (AD)+ plant in Holton, Suffolk. Now, this isn't just any old tale of fixing what's broken; it's a story of fitting digester mixers that have worked well elsewhere into an existing facility with a spark of ingenuity. It's brought a struggling plant back from the brink, and how!
In the heart of Suffolk, right next to the famous Bernard Matthews poultry facility, the Holton AD plant was in a bit of a state, with biogas production nearly ground to a halt. But, with a bit of determination and a canny eye for improvement, EVE has turned things around.
Stick with me, and I'll take you through how this plant went from zero to hero, showing the world how to get things done!
[boomdevs_toc]
Press Release 12 January 2024:
New Digester Mixers Produce Higher Biogas Production While Revitalizing a Troublesome Anaerobic Digestion Plant
Following an extensive upgrade of its reception tank and digester mixing system, Eco Verde Energy (EVE) has put a once troublesome Anaerobic Digestion (AD)+ plant firmly back on track with encouraging new biogas yields.
Challenges and Overhaul at Holton's AD Plant
At Holton1 in Suffolk, England, which receives around 65% of its feedstock from the adjacent Bernard Matthews poultry facility, the AD plant, under a series of different operators, had seen biogas production drop significantly, and eventually to a complete halt for a much-needed overhaul.
Identifying and Addressing Equipment Failures
Initially, the primary digester (2700m3) was drained down, discovering, as expected, faults with the mixers, but also a broken stanchion.
Further examinations found that the digester's roof had been damaged, therefore operations were postponed for a comprehensive repair and rebuild.
Critical Observations by Eco Verde's Site Manager
“The digester mixers that were sold in as part of the biogas package were never going to last in the long-term,”
said Eco Verde’s Site Manager at Holton, Kris Martin.
Struggles with Equipment and Industry Understanding
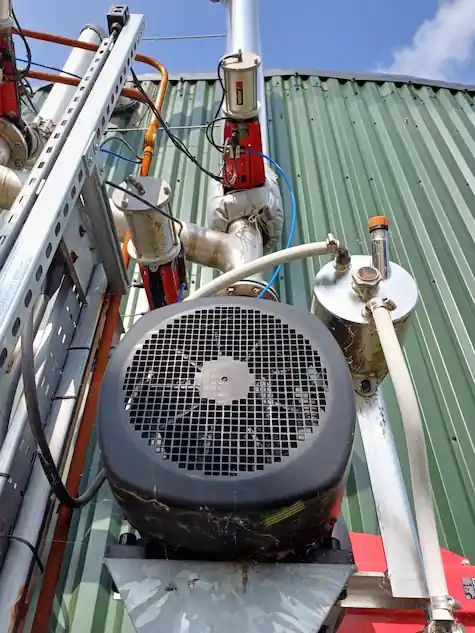
He added:
“At one point, the site was being run remotely, but it has now benefitted from a complete review of operations.
When we shut down for the maintenance overhaul, trying to get shipshape became more challenging, due to some suppliers not being able to assist; either unable to provide equipment quick enough for our needs, or did not seem to have a deep understanding of the industry.
Either way, the essential assistance we required was not readily available. We couldn’t for example, get anyone to look at the feed-in module (which is a jacketed tank to provide heat) we have between the reception tank and the digesters.
The previous chopping pump had failed because of the high temperatures, so again, it wasn’t specified properly.
There can be a huge difference in supplying equipment in 304 stainless steel compared to 316. For a biogas process with food waste, compromising is only going to lead to problems.
This has been the classic case of a package plant being sold on price rather than quality.”
Turning Point with Landia's Involvement
However, things improved significantly when Kris got into contact with Landia, about whom he had heard positive accounts.
Collaborative Approach to Finding Solutions
“Landia Clearly wanted to try and understand how a solution could be found”
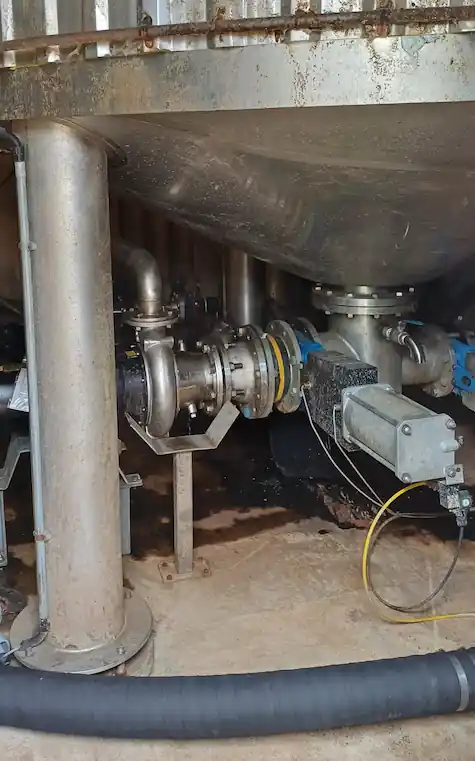
He continued:
“They’re a pump and mixer company, and there are plenty of those,”
he said,
“but unlike some others, they actually listened and clearly wanted to try and understand how a solution could be found. As soon as they first came to the site, there was a good vibe. Linking up the mixing operation from the reception tank, through the feeding module, and then on to the digesters, and finally through to the pasteurisers, wasn’t going to be easy.
But rather than just try and sell us equipment, Landia were keen to find a way to help make the Holton plant perform as it should.”
Upgrades and Improvements with New Digester Mixers
New Landia submersible digester mixers (5.5kW) have been placed in the reception tank.
Unlike earlier units, they can be simply hoisted up on a crimped rail system for examination to remove any plastics and perform normal maintenance such as oil changes.
Enhancing the Primary and Secondary Digesters
The primary digester was initially updated to replace failed units with Landia digester mixers.
These new 18.5kW digester mixers were installed with minimal disruption to the biogas process, thanks to the reuse of a pre-existing hatch system that allows for easy access. They can also now be maintained without incurring digester downtime.
Final Stages: Pasteurization and Biogas Production
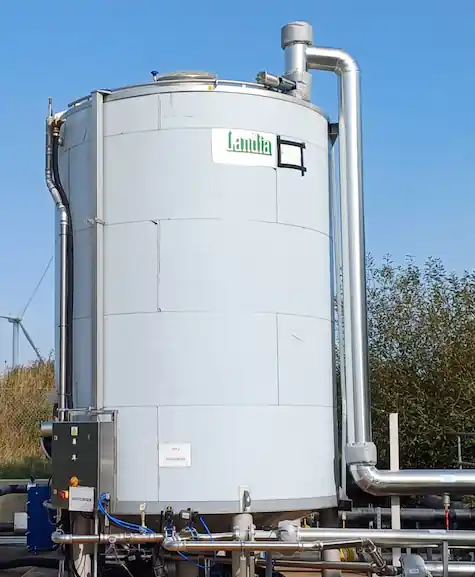
To meet the legal requirements of a feedstock containing animal by-products, there are now two (25m3) Landia pasteurizers that heat the final effluent to the required temperature of 70 degrees centigrade.
The pasteurisers are delivered as complete processing systems (tank, chopper pump, and controls) that break down food waste effluent and any leftover solids. Each Landia tank features a double stainless-steel tank wall that serves as a heating jacket.
From here, heat is transmitted via circulating hot water, therefore a stand-alone heat exchanger is not necessarily required.
After pasteurisation, with the maximum amount of gas eliminated, the final digestate from Holton produces a first-rate, nutrient-rich fertiliser.
Customized Solutions and Long-term Success
‘Nothing on this site is now off-the-shelf’
Kris Martin added:

“The more Landia and I worked together, the more we had a focal point. Although they do provide some guide rails and pipework, it’s not their main business. But when looking at how we could transfer everything from the start of the process, right through to the pasteurisers, it made sense for Landia to include it as part of their service, rather than me having to bring in another supplier.
They did a top-quality job in putting all the extensive pipework together. It’s very impressive and we’re all proud of it.
Nothing on this site is now off-the-shelf. Paul Broadhurst (from Landia) and I have put this all together step-by-step.
It’s not been easy, but we’ve worked through it with a very healthy rapport and that all-important common goal of wanting something to work and work well for the long term.
It’s a world away from the daily hassles that we had previously. Paul’s attitude to whatever we ask is ‘we’ll sort it out’, and I know he and Landia will because they value us as a customer and care about the plant’s success.”
Diverse Feedstock Management for Optimal Biogas Yields
In addition to its primary feed (which is first treated by a DAF (Dissolved Air Flotation) plant, and piped in from the treatment plant of the Bernard Matthews poultry facility.
EVE's Holton site also receives effluent from the local Adnams brewery and distillery, as well as various fats and oils from nearby food processing plants.
This type of feedstock intake necessitates very careful management to maintain a consistent feed for the now-popular biogas plant.
Stability and Efficiency in the Biogas Process
Kris Martin continued:
“With the Landia submersible digester mixers at the front end, we’ve gradually developed a constant, homogenous feed, which provides excellent stability for the remainder of the process and our drive to maximise biogas yields.
The consistency we have means happy bugs because otherwise, too much of one intake at one time can cause foaming. That’s not an issue at this site any more.”
Meeting Energy Needs and Focusing on Future Growth
The new-look Holton biogas plant (which now has two CHP engines and additional gas storage) can meet the majority of Bernard Matthews' 1.4MW energy requirements, with a grid connection in place for times when the poultry factory is shut down.
Benefits of Investment and Efficient Operation
‘Low energy consumption and maximum biogas yields’
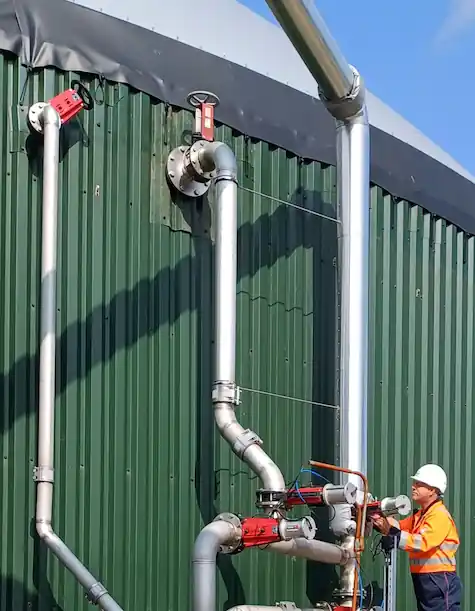
Kris commented:
“The investment here safeguards the future, with plans for a lagoon to be built and to have PAS 110.
With Landia’s help, it means that we’ll be in good shape with low maintenance costs, low energy consumption and maximum biogas yields, which of course means profit – not to mention the fact that we do something great by making renewable energy from waste.”
Achieving Operational Excellence and Industry Recognition
“Having to shut down and clean out a couple of digesters creates downtime of almost three weeks; costing in the region of £150,000.
“We’re pleased of course to have now sorted out all the problems; turning everything around so that instead of having put out fires, we can finally be proactive and concentrate on making gas, rather than having to react to all the problems on site.”
“The initial issues were made all the worse by having equipment that you couldn’t work on without having to shut the plant down! A design that effectively traps mixers inside the tank without access is ridiculous.”
Seamless Collaboration and Future Optimism
“We now have a proper maintenance schedule in place, and unlike in the past, no problems or delays in the availability and delivery of parts.
If we order before lunchtime, Landia delivers the next day. During installation, there were also never any problems with the paperwork and permits from Landia; progress emails, and all the necessary RAMS (risk assessment and method statement) and proof of qualification were in place so that the work was seamless, with no delays.
This differs significantly from others who simply aim to provide a product, without considering how it integrates into our process.”
Concluding Remarks on Biogas Plant Success
“Site managers can overcome all sorts of challenges, but aren’t necessarily engineers. You need calculations. You need experts to answer your questions to complete the jigsaw puzzle.
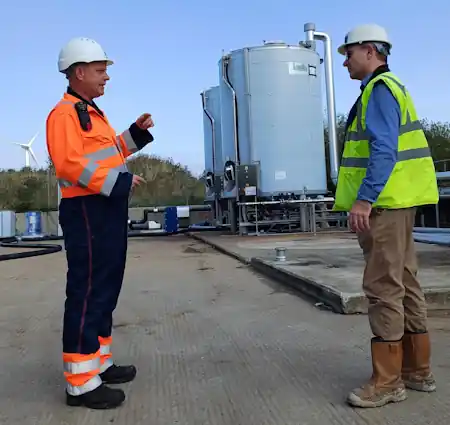
No two plants are the same. It is reasonable to expect seamless support from the companies that provide equipment, but often, you find yourself navigating through various departments – from quotations to finance, engineers, and a loosely termed ‘support team.’ Having to repeatedly explain your requirements can be very frustrating and time-consuming.
It is always easier to work with those who have been to a biogas plant, and who aren’t worried about getting their hands dirty.
It’s been a long journey to get where we are, but we now have peace of mind with a plant that is performing very well and with fine-tuning, will get even better. It shows exactly what can be achieved with the right people, the right equipment, and a belief in our industry.”
About Privilege Finance
1 The Holton plant is owned by Privilege Finance, a speciality funder with over 20 years of experience funding carbon-reduction and climate change mitigation projects.
Privilege has granted over £600 million in funding to power one million UK homes with green energy.
Privilege not only provides financial solutions and knowledge, but it also develops, owns, and runs renewable energy projects, and has skilled sales and technical delivery teams working throughout the UK.
Privilege, based in Cambridge, collaborates closely with clients using a whole ‘project lifecycle' strategy, providing support services to ensure seamless project delivery, commissioning, and optimisation.