In this article, we have set out to explain industrial load testing, and realise it or not, it means that Biogas Plant Operators have one less hazard and one less headache to worry about. Read on and find out how industrial load testing ensures that the heavy equipment used at anaerobic digestion facilities can stand the loads it is subjected to.
Steel biogas tanks and roofing can be used with confidence, and (pumps, mixers, etc.) can routinely be lifted and handled, without the significant risk that structures and lifting gear will fail and cause injury, all due to industrial load testing.
The Hidden Engineering Discipline That Keeps Biogas Plants Safe
When biogas plant operators survey their facilities—watching digesters churn, monitoring gas production, or overseeing maintenance schedules—industrial load testing never crosses their minds. Yet this invisible discipline operates behind the scenes of every successful anaerobic digestion operation, silently ensuring that steel tanks won't buckle under pressure, that crane systems can safely lift heavy equipment, and that structural components won't fail catastrophically during routine operations.
Industrial load testing represents one of the most sophisticated yet overlooked aspects of biogas plant design and operation. While operators focus on feedstock management, gas yields, and process optimisation, a cadre of specialised engineers works in the shadows to guarantee that every beam, joint, and lifting mechanism can withstand the demanding loads placed upon them.
These experts walk a precise tightrope—specifying materials strong enough to ensure absolute safety, yet not so overengineered that they burden projects with unnecessary costs that could cripple the economics of anaerobic digestion facilities.
This hidden discipline has quietly revolutionised how the biogas industry approaches structural integrity, transforming what was once educated guesswork into precise science.
The result?
Plant operators can sleep soundly knowing that their most critical infrastructure has been rigorously tested to perform under the most demanding conditions.
At the same time, project developers can optimise costs without compromising safety—a delicate balance that makes the difference between profitable biogas operations and financial disasters.
What is Industrial Load Testing?
The quality of equipment used by businesses and companies who operate in the heavy-lifting industry is important. It is crucial to the protection of their assets, the safety of workers and to meeting set standards and industry regulations.
Having unsafe equipment implies that the business is falling short of required standards. This can result in accidents, injuries and even the death of employees. It will also lead to inefficient operational processes and negatively impact the company in many other ways.
This is why carrying out tests as well as inspections on your equipment are important. It helps to ensure that they are safe. Many kinds of tests can be conducted on a piece of equipment. One of these is called load testing. You will find some other kinds of tests that can be conducted in this article.
A Little About Industrial Load Testing
Load testing is a way of putting demand or pressure on a system so as to measure its response. These kinds of systems can be a structure or a piece of equipment. Pressure in form of stress is applied to the structure or equipment and this helps to determine its load-bearing capacity.
Some of these structures can include cranes, bridges, elevators, gantry, jib cranes, monorails and other types of load-bearing equipment. What the test will determine includes:
- Safe working load (SWL): This is the recommended maximum stress it can bear.
- The Yield Load – This is what it can bear to the point where the materials begin to show signs of degradation or stress.
- Failure Load – This is the point at which the structure breaks down or there is a complete mechanical or material failure.
The overall purpose of the process is to verify that all components of a structure are fit for whatever it is designed for. These components include the materials it is made of as well as its base fixings. The technical specification or test method of the equipment will contain details about the test.
There are several types of load testing techniques that may be employed. These are:
Static Testing: This is when a perpetual load is exerted for a specified period. This technique applies uniform tension at a slow rate.
Dynamic Testing: This involves applying a moving or variable load. Dynamic testing exerts tension rapidly through increased speed or sudden stress spikes.
Cyclical Testing: This involves repeated loading and unloading at specified durations, cycles and conditions. The stress may include various levels of load at drastic temperature changes.
Types of Load Testing
Different types of load tests can be carried out on a structure or equipment. These are:
Tensile Tests
This involves subjecting a sample to uniaxial tensile force until there is a failure. This test helps to measure the tensile strength and also the maximum elongation as well as a reduction in area.
Proof Tests
This test requires a component or structure to demonstrate its capability to bear stress at a specified safe working load. You may read more on this test here https://www.crownroundtable.org/proof-load-testing-is-it-necessary/.
Shear Tests
This test is used to determine a component’s maximum shear stress before it experiences a sliding failure. This is done on the plane of an object, which is perpendicular to the applied force.
Compression Test
This involves subjecting samples to a compressive force. This helps to determine the crush resistance of the material during a specified period.
Fatigue Test
A fatigue test is used to determine the behaviour of a material. This is done under alternating stresses or strains. It is a series of cyclic tests and it simulates conditions where a material or components undergo various cyclic forces.
Impact Testing
This tests the material’s ability to absorb energy at high-stress rates.
Fracture Toughness
This tests a material’s ability to withstand uniform propagation of stress under certain known loading conditions.
Bending Tests
A bending test measures a material’s elasticity as well as strength. When the bend is completed at the desired angle, the material is inspected for cracks on its outer surface.
Bond Strength Test
This involves determining the stress that is required to bring about an adhesive bond fracture between two materials. A bond strength test can be performed in a lab environment or field.
When to Perform Loading Tests
This test is performed to meet certain standards that are set out by the government or industry regulations. It should be undertaken during the manufacture of equipment and before it is put into use for the first time.
It may also be required when a major component is replaced or after a major repair has been carried out on equipment. These include any mechanical or structural modifications. Testing may also be carried out at regular intervals to determine the continued compliance of a system.
Undergoing regular testing and inspections is important to ensure your equipment remains safe. The testing should be carried out by qualified professionals who are skilled at detecting defects or any issues. Doing this would ensure that it operates as it should.
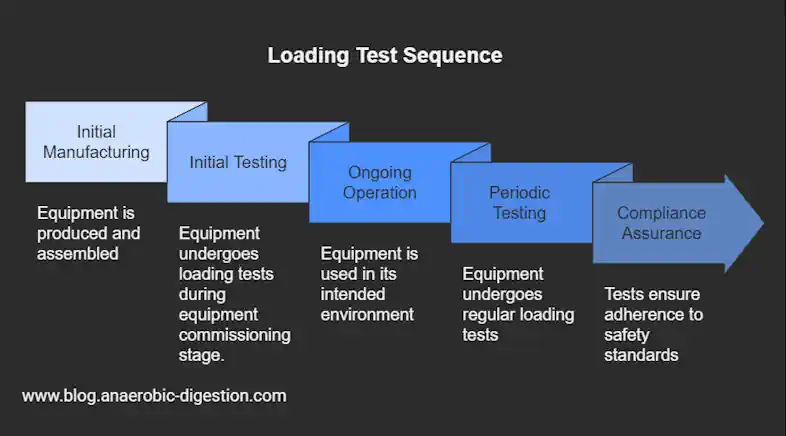
How To Carry Out Load Testing
Some companies provide various forms of industrial load testing services. They offer this to other companies that need to determine the load-carrying capabilities of their equipment, components, or structures. A certificate is then issued after the test has been carried out.
These companies make use of various equipment to determine this. These can include water bags, sledges, rigging, as well as certified carts and weights. They typically have the experience and expertise to produce accurate results.
They may sometimes rent out this equipment so that people who need it for a limited period can use it. This helps to lower their project budget. They can also provide an on-site operator who helps to monitor how the test samples react to various loads. Aside from this test, other inspections such as structural checkups, welding inspections, visual inspections and more may be carried out.
Conclusion
Load testing is an important process to ensure the safety and efficacy of a structure or equipment. It helps to determine the capability of the equipment to see if it works as it should. It is therefore important to carry out these tests to avoid accidents and to comply with industry regulations.