Understanding how to measure biogas accurately can be a puzzling task for many. Did you know that measuring it requires specialised techniques due to its composition and flow rates? This article will provide you with a step-by-step guide on how to measure both the quality and quantity of biogas effectively.
Let’s explore this valuable energy source together!
Key Takeaways to Remember About How To Measure Biogas
- Biogas is a renewable energy source made from breaking down organic waste without air which results in a mixture of gases, dominated by methane. In its raw state, it is usually saturated with water vapour and contains varying corrosivity, and when siloxane is present may produce a deposit which can be damaging to equipment exposed to it.
- Measuring biogas quality and quantity is important for knowing its energy value, identifying issues in the production process, and determining its monetary worth.
- Techniques like flame ionization detector (FID) gas analysis and infrared technology can be used to accurately measure biogas quality, while flow meters are routinely used to measure biogas output flow rate.
- Challenges in measuring biogas include ensuring accuracy and reliability, dealing with contaminants and corrosivity, monitoring hydrogen sulphide levels, and determining quality.
[boomdevs_toc]
What Complicates Biogas Measurement?
Because biogas is a renewable energy source produced through the decomposition of organic matter, and inevitably this results in a mixture primarily composed of methane and carbon dioxide. The constituents of the biogas vary continually as the microorganisms that make it adapt to changes in the incoming feed materials.
This makes biogas measurement more complicated than simply measuring a gas flow.
Not only is it necessary to monitor the flow it is also necessary to know what proportion is methane and to continuously adjust the calculation of the value of the methane gas present.
1. How To Measure Biogas for its Gas Chemical Content
The Chemical Components of Biogas
As we have said many times before on this website, biogas is a clean and renewable type of energy. You make it by breaking down organic stuff without air, like plant waste or animal poop. This process is called anaerobic digestion or is very loosely referred to as fermentation.
The gas you get has about 50-70% methane and 30-40% carbon dioxide in it. Small amounts of other gases are also there.
Let us not forget that using biogas helps us to take good care of our Earth because we can reuse farm, city, and food waste to create power! For this and other reasons, the use of biogas is a great step towards a world that does not rely on coal or oil for energy.
Reasons for Measuring Biogas Output Volume and Quality
The act of checking biogas quality and how much is made has good reasons. Top of the list is knowing its energy worth. High or low, energy value shows us if we can use biogas for heat, electricity, or as car fuel.
Next up, it tells us how well the making process is going. If there's less gas or poor quality, something may be wrong with the steps taken to make it. Also important is keeping track of what goes into making biogas like waste from farms and towns or plant stuff since each gives a different result.
And let's not forget money matters – knowing the amount and kind of biogas put out helps figure out its cash value too! Accuracy also matters. Even a consistently small error in one direction may mean either the seller or the buyer unfairly losing out on a lot of money.
Biogas Quality Measurement Techniques
Gas analysis is the term used for the techniques used to measure biogas quality, where the composition of gases such as methane, carbon dioxide, and hydrogen sulfide are analyzed.
Laboratory Based Gas Analysis
Gas analysis, carried out on samples delivered to accredited testing laboratories is a key part of checking biogas quality. Here are some steps to follow:
- Use a recognised gas analysis testing standard for the job. Using a recognised test protocol (method) tool gives exact data about the gas makeup which can be replicated in other labs.
- Do not forget that things like heat changes and vapour can change your results.
- Know that other ways do exist to check your biogas output, such as looking at digester size to check the calibration of the results you obtain.
- Keep in mind that batch tests on multiple samples obtained over a period of time might be more representative of a varying digester output than using just one test result.
Continuous Gas Quality Measurement Using infrared technology
Infrared technology plays a big role in testing biogas quality alongside flame ionisation detection.
Tools like the IR15TT-R dual gas infrared gas sensor help find out how much flammable gas and carbon dioxide are in the biogas.
You can trust this method because it's reliable and works well. Some companies make special tools for this, like MRU Instruments' biogas analyzers. These work all the time to keep track of what is in the biogas.
Science acks up using infrared technology, as seen with infrared spectroscopy that measures digestion process parameters. So, when you need to measure your biogas flow and quality, think about using infrared tech!
Measuring methane content
Methane content in biogas is important. We need to measure it. The usual way that biogas plant operators check methane is by applying EN ISO 25140:2010 and EN ISO 25139:2011 rules.
ISO 25140:2010 defines the principle, key performance criteria, and quality assurance and quality control procedures for an automatic method of detecting methane in stationary waste gas using flame ionisation detection.
ISO 25139:2011 defines a manual technique for determining methane emissions concentrations from stationary sources.
They make sure the measurement is right by giving clear steps to follow. Through the use of accreditation bodies, the results of each lab are checked for accuracy. All these methods give us good ways to get the gas monitoring data needed in order to get the best out of our biogas plants.
Overcoming potential errors in gas quality measurement
It's crucial to fix errors in biogas measurement. Here are some ways to do it:
- Use the right calculation methods. Errors can occur if the wrong methods are used for temperature correction in weight gasometers or column height.
- Watch your biogas plants closely. This helps to spot issues that may cause overload and acidification, such as changes in feedstock mix or wrongly measured inputs.
- Pick the best measuring methods. Studies show that certain ways of measuring total biogas and methane production work best.
- Understand what affects biogas production. Factors like the type and amount of biomass used, digester size, and temperature can affect how much biogas is made.
- Check for a match between on-site methane yield and calculated specific methane potential (SMP). These should line up if you use biological degradability assessment methods correctly.
- Keep studying and learning about possible errors in biogas measurement, and analysis, and their link to anaerobic processes.
2. How To Measure Biogas Flow Rate
Different techniques are used to measure the flow rate of biogas and the biomethane produced after purity “upgrading”. These vary from the use of traditional paddle gas meters and non-pipe intrusive ultrasonic flow meters.
What is a Flow Meter?
A flow meter, or flow sensor, is an instrument designed to precisely measure the flow rate in a pipe, aiding in ensuring safe, efficient, and environmentally compliant operations in various applications.
Read on to learn how these techniques work and their pros and cons in accurately measuring biogas output.
Types of Gas Flow Meters:
- Electromagnetic Flow Meters: Uses Faraday’s Law of induction to detect flow changes.
- Pros: No pressure loss, no moving parts, reliable, and unaffected by liquid properties.
- Cons: Can't measure gases/liquids without conductivity and needs straight pipe sections.
- Applications: Food, chemicals, natural gas, power utilities.
- Vortex Time Flow Meter: Uses the von Kármán effect principle to measure flow rates.
- Pros: No moving parts, versatile application, little pressure loss.
- Cons: Sensitive to vibrations and flow velocity shocks, straight pipe requirements.
- Applications: Power generation, compressed air, steam.
- Paddle Wheel Flow Meter: Turbine meter measuring flow from paddle revolutions.
- Pros: Reliable, low-cost, bi-directional measurement.
- Cons: Requires clean fluids and turbulent flow profile.
- Applications: Fume scrubbers, reverse osmosis.
- Thermal Dispersion Mass Flow Sensor: Measures flow rate using temperature differences.
- Pros: Accurate, no moving parts, bi-directional measurement.
- Cons: Unsuitable for high-temperature gases or liquids.
- Applications: Medical devices, gas monitoring systems.
- Floating Element Flow Sensor: Simple technology using a float in a tapered pipe.
- Pros: Cost-effective and easy to use.
- Cons: Manual measurement, not for high flow rates.
- Applications: Chemicals, compressed air.
- Ultrasonic Flow Meter: Utilizes ultrasound and the Doppler Effect.
- Pros: No moving parts, high accuracy, low maintenance.
- Cons: High cost, dependent on fluid properties.
- Applications: Process to custody flow.
- Differential Pressure Flow Meter: Uses Bernoulli’s equation to measure flow via pressure differences.
- Pros: Accurate, reliable, no moving parts.
- Cons: Not for liquid measurement, requires pressure drop.
- Applications: Power supply, food, aerospace, HVAC.
- Coriolis Mass Flow Meter: Vibrating tube measures flow-induced frequency changes.
- Pros: True mass flow measurement, unaffected by other properties.
- Cons: Moving parts, sensitive to environmental vibrations.
- Applications: Industries needing sanitary/corrosive gas measurements.
Summing up on the flow techniques
There are many ways to measure biogas flow. One promising tool is a thermal mass flow meter. This gadget measures the mass flow of gas.
The crucial variable for the biogas plant operator is the gas value and mass, not volume, because volume varies with gas pressure. Because of the effects that variations in temperature or pressure have on the density of a fixed volume of gas, volumetric flow measurements are less trustworthy than mass flow measurements.
Thermal mass flow metres are immune to variations in the temperature and pressure of the incoming flow, unlike volumetric flow measurement devices such as purge metres (variable area metres) or turbine metres. The mass flow metre can give direct mass flow measurement.
Most other methods detect volumetric flow and require independent temperature and pressure measurements, plus a knowledge of the %age methane content, to calculate density and, ultimately, mass flow.
Lastly, automatic volumetric gas flow meters work well for checking biogas output in small lab-size digester units. In such cases, the technician may use an FID device to monitor for the methane content in the biogas.
Pros and Cons of the Techniques Used
Deciding on the most suitable technique for measuring biogas is important, especially when considering factors such as accuracy, cost, ease of use, and the potential for error. Below is a table evaluating the key pros and cons of the most common biogas measurement techniques:
Technique | Pros | Cons |
---|---|---|
Laboratory Gas Analysis | Provides accurate measurements of gas composition on samples collected manually. It is an accurate way to determine the methane content, an essential element in biogas. | The lab analysis is complex and requires specialist equipment and training. Long waiting time to see the results from each sample submitted. It is expensive. |
Infrared Technology | Non-contact method, which offers quick and accurate measurements. It can measure various gases without the need for sample extraction. | It requires advanced equipment and may be costly. Infrared sensors may not be precise with low-concentration gases. |
Measurement using Ultrasonics | It can be a reliable technique for volume measurement. It enables continuous tracking of biogas production over time. | It requires advanced equipment and may not accurately account for temperature and pressure variations. |
Flame Ionisation Device | This is a simple and, once the FID device has been paid for, cost-effective technique. It is great for portable instrument use by small-scale biogas producers. | It needs skilful recalibrating and for that reason may not accurately reflect ongoing production levels during continuous monitoring. |
These techniques have unique attributes that make them more suitable for certain situations. Consideration of factors such as the size of the operation, available resources, the desired level of accuracy, and safety requirements should guide the decision on which technique to adopt.
Challenges of Biogas Measurement
Accurate biogas measurement faces challenges such as ensuring reliability, dealing with contaminants and corrosivity, monitoring hydrogen sulphide levels, and determining quality. Discover how to overcome these obstacles for efficient biogas production.
Accuracy and reliability
Accurately measuring biogas is crucial for the efficient operation of biogas plants and optimizing energy production. However, it can be challenging due to variations in the concentrations of different gases in biogas.
Measurement errors can occur due to factors like temperature changes and vapour content. To ensure accuracy and reliability, flow meters are considered the most accurate way to measure biogas consumption.
Methane and CO2 concentration measurements are also essential for evaluating the anaerobic digestion process. By accurately measuring biogas, operators can monitor production stages, optimize fuel sources, and monetize their biogas efficiently.
Contaminants and Corrosivity
Biogas can contain contaminants like hydrogen sulfide, which can cause corrosion in equipment. This is a challenge for plant operators and engineers who need to ensure the smooth operation of biogas systems.
The composition of biogas can vary, making it difficult to accurately measure the wide range of trace contaminants present. It's important to monitor and control these contaminants to prevent damage and maintain the efficiency of biogas production.
By taking measures to remove or minimize corrosive elements, operators can ensure the longevity and reliability of their biogas plants.
Monitoring Hydrogen Sulphide Levels
To ensure the safety and proper functioning of biogas plants, it is important to monitor hydrogen sulphide levels. Hydrogen sulphide is a toxic gas that can be produced during the anaerobic digestion process.
It poses health and safety risks to plant operators and can also cause corrosion to equipment like co-generators and compressors. By monitoring hydrogen sulphide levels, plant operators can take necessary measures to prevent these risks.
One effective method for monitoring hydrogen sulphide levels is by using the OMA system, which utilizes dispersive UV-Vis spectrophotometry. This system has a dynamic range that makes it suitable for measuring hydrogen sulphide in biogases.
Summing up on biogas quality determination
Several techniques are used to determine biogas quality, including laboratory gas analysis and measuring methane content continuously in the pipe flow. Monitoring hydrogen sulphide levels is also crucial, as this compound can be toxic and harmful to equipment.
It is only by accurately determining the quality of biogas, that operators can ensure that it meets industry standards, avoid potential issues with corrosion or contamination, and maximize its potential as a sustainable energy resource.
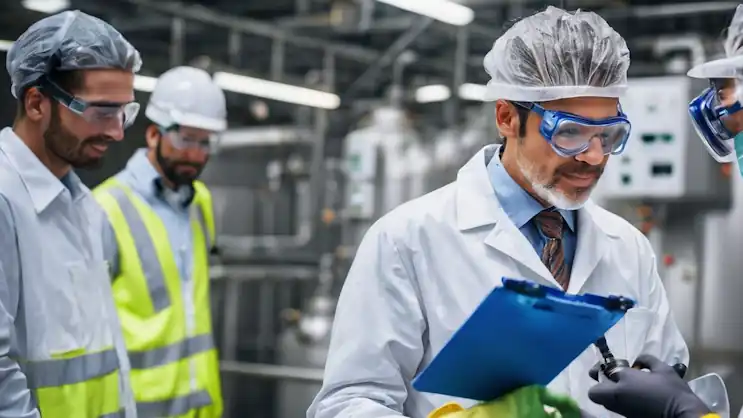
The Importance of Precise Biogas Measurement
Precise biogas measurement is crucial for monetizing biogas, ensuring efficient fuel sources, and monitoring production stages.
Monetizing biogas
Biogas has the potential to be a valuable source of income. By monetizing biogas, operators of biogas plants and anaerobic digestion systems can turn it into a profitable venture. Biogas can be
- used as an alternative fuel source with a premium value for vehicles or
- sold by upgrading to biomethane and with pressurization injected into the gas grid as renewable methane energy.
By efficiently measuring and monitoring biogas production, operators can optimize their processes and increase their revenue potential. This is especially important considering that biomethane is the most cost-effective form of renewable gas available today and that the European biogas industry is rapidly growing.
So, by accurately measuring biogas output volume and quality, operators can ensure they are maximizing its value while contributing to a more sustainable future.
Monitoring production stages
Monitoring the production stages of biogas is crucial for plant operators and owners to calculate the biogas yield per unit of organic material input, allowing them to optimize their resources.
Additionally, sensors and monitors are essential at each stage of the production process to maintain equilibrium and maximize output.
Through continuous monitoring and control, plant operators can improve efficiency and better understand how anaerobic digesters behave. This helps in maintaining a steady flow of biogas while minimizing any disruptions or issues that may arise during production.
Conclusion to “How To Measure Biogas”
Measuring biogas is crucial for assessing its quality and quantity.
Various quality measurement techniques such as laboratory gas analysis and continuous infrared technology measurement can be used to measure its quality accurately.
Measuring the flow rate of biogas with its quality in terms of the methane content and the absence of unwanted substances allows its value to be recorded, and is not least used in charging for the output which is sold. At the same time helps in optimizing the operation of the AD plant and its energy production efficiency.
Despite challenges, precise measurement is important for monetizing biogas, ensuring efficient fuel sources, and monitoring production stages. By employing these measurement methods, operators can maximize the benefits of biogas production while minimizing potential issues.
How To Measure Biogas FAQs
1. What is biogas?
Biogas is a kind of gas made by breaking down things like animal waste or plants without air.
2. What is the simplest way to measure biogas flow and quality?
The simplest way to continuously measure biogas quality and flow is by using advanced instruments like the Proline Prosonic Flow B 200 ultrasonic flowmeter.
This device employs ultrasonic technology to measure both the flow and composition of biogas, ensuring a high degree of accuracy and reliability. Ultrasonic flowmeters work by sending and receiving ultrasonic waves between transducers, with the flow rate determined based on the time it takes for the waves to travel.
Additionally, the Proline Prosonic Flow B 200 can determine the methane content of the biogas, providing insights into its quality. Its non-intrusive measurement ensures there's no pressure loss or potential for leaks. With capabilities like real-time monitoring, automated data recording, and remote access, such devices help to ensure continuous, efficient, and safe biogas production and utilization.
3. Can I learn how to measure biogas flow?
Yes, you can use certain tools to see how fast the biogas moves through a pipe or space.
4. Why should we measure biogas flow and quality?
Measuring biogas flow and quality is crucial for up to 10 key reasons. Here are just a few. First and foremost, it ensures safety by monitoring methane concentrations to prevent flammable risks. It optimizes energy production, allowing systems to work efficiently and produce maximal energy output. Monitoring is essential for environmental compliance, ensuring that methane releases meet regulatory standards. Economically, it ensures maximum revenue generation from the biogas, either sold directly or used for electricity sold to the grid.