Disposing of unwanted whey from commercial dairies, was once a considerable problem. But, that was before recent developments in the anaerobic digestion of whey and biogas plant technology. Instead of a problem whey which is not for any reason suitable for food production has become an asset.
During the anaerobic digestion process microorganisms break down the organic materials in whey and convert them into gases (biogas), including methane, carbon dioxide, and hydrogen.
The resultant biogas can be used for cooking or heating purposes or upgraded as a substitute for natural gas. Anaerobic digestion is a closed system so there are no emissions released into the environment during the process.
Read on for more details:
The Problem with Whey
The problem with whey is that it is a byproduct of the process of making cheese and other dairy products. It can be used as animal feed, but not all whey is safe for this use.
In order to make sure that the whey is safe for animal consumption, it must be heated to a certain temperature and pressure. If it isn't then the bacteria in the whey can cause illness in animals and humans.
It is a watery liquid that is left over when milk is curdled and strained to make cheese. Whey can be used as an ingredient in many other processes, such as bread making or animal feed. However, there were many problems with whey disposal and treatment, until the use of the anaerobic digestion process became common.
The most common way to dispose of whey in the past was to dilute it with water and then release it into a body of water such as a river or ocean. However, this poses many environmental problems for the environment because it can lead to oxygen depletion in the water and harm aquatic life.
Another problem with whey disposal is that, unless it is digested to produce biogas, it often ends up going straight into landfills where it takes up space without being recycled or reused for any purpose whatsoever.
A final issue with whey treatment involves how much energy goes into creating this byproduct in the first place. The process of making cheese requires significant energy input. However, adding a biogas plant fed by whey (and usually other organic wastes as well) can be a perfect way to create the needed renewable energy on-farm.
The Problem with Landspreading Waste Whey
Farmers can use only limited amounts of the nutrient-rich liquid. If they put too much of the whey on their land, the mixture will run off into nearby waterways, leading to:
- algal blooms,
- low levels of dissolved oxygen, and
- fish kills.
What’s more, “acid whey” can emit a stench when baked in the hot sun, leading neighbors of some farmers to complain about the smell. via cen.acs.org
What is Whey?
Whey is the liquid material created as a by-product of cheese production. Whey is left over when milk is coagulated during the process of cheese production, and contains everything that is soluble in milk after the pH is dropped to 4.6 during the coagulation process. It is a 5% solution of lactose in water and contains the water-soluble proteins of milk as well as some lipid content. Wikipedia
/soc_panel]
Renewed Interest in the AD Process of Composting Without Air Proves a Great Solution for Whey Disposal
In recent years Anaerobic Digestion has become a competent technology for the biological conversion of organic content of Dairy Wastewater.
The dairy industry generates whey which is the most important wastewater produced, with an extremely high organic load (50-70 g/lit COD).
Cheese whey as a by-product of the dairy industry consists of carbohydrates mainly lactose, lactic acid, proteins and fat, etc. In the anaerobic digestion of whey it is initially hydrolyzed and converted to organic acids by acidogenic bacteria then the degradation is followed by the methanogenic bacteria.
The anaerobic digestion process has a number of advantages; one of them is the production of methane as an energy source which consists of 50 to 70 % methane. via semanticscholar
Biogas to Grid was the “Whey” to go for Cumbrian Cheese Maker
Berkshire, UK-based anaerobic digestion specialist, Clearfleau, has commissioned several AD plants to supply the UK gas grid, from the anaerobic digestion of whey, with biogas generated purely from cheese production waste.
The company said that one facility, located in rural Cumbria, was its most complex plant to date (in 2019) and would feed biomethane into the gas grid.
According to the Clearfleau announcement, by feeding the biomethane into the grid, the facility will generate over £3 million per annum in cost savings and revenue, while supplying up to 25% of the creamery’s energy requirements.
The New “Lake District Biogas” AD Plant
The plant has been designed and built for Lake District Biogas, which will operate the site for 20 years taking feedstock from First Milk’s Aspatria creamery site.
First Milk is a dairy company owned by family farms which supply it with fresh milk. In turn, it supplies cheese, dairy products and ingredients to the retail and food service markets in the UK and internationally.
Feedstock of Cheese Production Residue After Protein Extraction
The whey feedstock is said to comprise low-strength wash waters such as process rinses, supplemented by whey permeate (cheese production residue after protein extraction for use in energy supplements), which is pumped to the Anaerobic Digestion of Whey plant from the creamery.
The liquid is then pumped into the AD plant from the creamery where the bugs convert the fats and sugars in the feedstock into biogas.
“First on-site Anaerobic Digestion (AD) plant in the dairy industry in Europe with Grid Injection of Biomethane”
The company has claimed that this is the first on-site Anaerobic Digestion (AD) plant in the dairy industry in Europe to inject biomethane into the gas grid. This is created exclusively by digesting its cheese-making residues.
Operating at full capacity the plant is expected to treat 1,650 cubic metres of process effluent and whey per day and generate around 5MW of thermal energy.
Multiple Outputs – Heat, Biomethane, Fertilizer etc
It is also expected to produce 1000 cubic metres of biogas per hour, of which over 80% will be upgraded for injection into the national grid. At least 60% of the biomethane will be used in the creamery for steam generation, with the balance being used by local businesses and households in Aspatria.
AD Plant Liquid Output is Further Treated Aerobically
Downstream treatment will take place in an existing aerobic plant which Clearfleau has upgraded and enhanced through the provision of chemical treatment for nutrient removal.
Reduced Levels of Phosphate in its Effluent is a Welcome Side-Effect
According to the company, this upgrade will allow First Milk to significantly reduce levels of phosphate in its effluent, which is discharged to the River Ellen. Supported by the Environment Agency, is expected to ensure early delivery of new tighter discharge standards, which are required by the Water Framework Directive.
Reduced Chemical Oxygen Demand (COD) in Production Residues Provides Another Benefit
Clearfleau’s added that its on-site AD technology is proven to reduce the Chemical Oxygen Demand (COD) of the production residues by at least 95%. Aerobic polishing will then remove residual COD and nutrients (nitrates and phosphates) to allow safe river discharge.
The residual sludge from the plant will be spread on local farmland as a nutrient-rich soil improver. via waste-management-world.com
The article below is our original article posted on 7 April 2012:
Anaerobic Digestion of Whey Story – The Little Miss Muffet Connection?
Anaerobic digestion of whey may become routine (but not for Little Miss Muffett!). As the move toward universal adoption of the Anaerobic Digestion process gathers in momentum, one thing is becoming clear. Mix it with slurry.
What is clear is that there are many more anaerobic digestion synergies than were first apparent, and this is one such!
According to the following Dairy Farm biogas article, where they have an excess of whey which is otherwise hard to dispose of, the mixing of this the “Little Miss Muffet” product with the farm manure is the big synergy story.
Read the quotation from the original article below to find out why that is. (And – Do you think that the Little Miss Muffet reference in the title was a bit too tenuous though… I did but it is in the original title!)
Paging Little Miss Muffet: Energy from Cheese Waste
Some farmers take recycling to the extreme, to the benefit of both the environment and their bottom lines.
They are the often-unheralded pioneers of waste-to-energy technology, sometimes powering entire small towns with their byproducts. The most common waste-to-energy method is to employ methane-excreting bacteria in anaerobic digesters. These turn farm waste like cow manure and rotting vegetables into biogas to heat their property and even sell electricity back to the grid.
For dairy farmers making cheese, however, the process can get tricky. Getting rid of the huge quantities of cheese whey — the byproduct of the cheese-making process — is difficult.
Digester Stability Solution “Mix the Whey with Cow Slurry”
That's because the whey matrix is rich in fat and tends to rapidly acidify. That makes it unstable in anaerobic digestion reactors.
Some farmers spread the whey on their fields as fertilizer, but depending upon the size of the farm, they quickly run out of field space to distribute the stuff.
“It’s a real problem,”
said Elena Comino. She is an applied ecologist at the engineering department of Politecnico di Torino in Italy.
Now Comino and her colleagues have proposed an easy solution in a recent study. That is to just mix the whey with cow slurry, commonly known as liquid cow manure, to get the right pH balance.
Anaerobic Digestion of Whey Provides Waste to Energy
Outside of nursery rhymes, whey doesn’t come up a lot in most people’s daily lives. But it is a plentiful waste product – there are only 100 dairy farms in the U.S. that produce relatively large volumes of cheese and every one of them creates millions of pounds of whey in a single year.
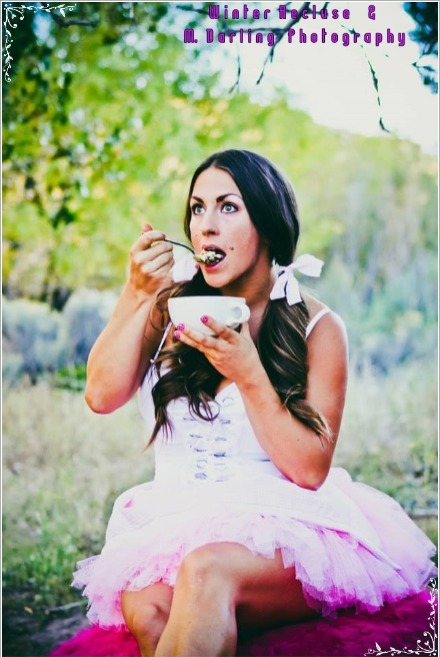
Figuring out what to do with all of this waste can be a challenge. To figure out the perfect biogas-producing concoction to optimise the anaerobic digestion of whey, the Italian researchers tried mixing different proportions of whey and cow slurry.
Through trial and error, they found that a 50-50 mix of slurry and whey yields a methane concentration of about 55% in the biogas.
This figure compares favourably with the energetic potential associated with the digestion of high-energy crops like maize.
“We obtained the most convenient mix in order to produce the best biogas in terms of quantity and quality,”
Comino said that before their study work;
Few experiments have examined the biogas potential of co-digestion of slurry or manure with whey mostly because in the past anaerobic digestion was mainly used for wastewater treatment.
But the technology is becoming more popular in Europe and North America since it benefits the environment and is an additional source of income for farmers.
“Cheese whey is a waste, but if you put it in a digester you can produce biogas so it becomes something you can reuse,”
the fan of anaerobic digestion of whey, Comino, said.
Anaerobic Digestion of Whey Can Mean No More Lagoons
In the past, the standard practice was to keep agricultural waste like cow manure was kept in an open-air lagoon before spreading it on fields as fertilizer. During this process, methane—a potent greenhouse gas—and other pollutants were released into the air.
Worse still, rainfall could cause the manure to run off and contaminate local waterways. On hot days, the manure smelled awful.
With a digester, rather than being left out in the open, the manure and whey are kept in a closed container, preventing greenhouse gases from entering the atmosphere and further exacerbating global warming.
Biogas is instead used as a renewable substitute for natural gas, propane or other fossil fuels. As for the digestate byproduct, it can be used or sold as fertilizer.
Although European farms currently lead the way with anaerobic digesters, subsidies from the state and local governments in places like Pennsylvania and Vermont are increasing the affordability for U.S. farmers to install digesters.
In the U.S. (circa 2019), there were around 160 anaerobic digesters on farms. Digesters number into the hundreds of thousands to a million for the rest of the world, according to the American Biogas Council.
Anaerobic Digestion of Whey Can Mean Selling Back Energy to the Grid
Some U.S. farmers are ahead of the curve in their anaerobic digestion of whey. Charley Crave owns Crave Brothers Farm and Farmstead Cheese in Wisconsin and has been recycling cheese whey for years.
He estimates that he produces about 20 million pounds (10,000 tons) of whey a year.
He loads both cheese whey and manure into the digester and says he doesn’t have “a scientific recipe” for the proportions he uses. He added that the types of cheese he produces, like fresh mozzarella, which he sells to Whole Food stores, are naturally low in acidity.
Crave said (circa 2019) that there were only a handful of dairy farmers in all of North America who use digesters to process whey.
Small dairy farms usually don’t have a cheese factory on their farm and so would have to transport their whey back to the farm to digest it. Perhaps more significantly, installing a digester can cost hundreds of thousands of dollars. After the initial installation cost, however, the digester begins to give back in a big way…
Please visit the original website to read more at Paging Little Miss Muffet: Energy from Cheese Waste. [original article no longer available.]
Watch the video below, to find out more about opportunities for farm biogas production.
[Published 7 April 2012. Updated 3 July 2019 and 17 December 2022.]
What’s the amount of whey and inoculum for biogas production? I am doing this project and I need these information immediately.
It’s not like baking the perfect loaf of bread to produce a product. One thing you will learn is that with biological processes, fed using mostly waste organic materials it is a case of blending them to satisfy a variety of nutrient requirements. The carbon-to-nitrogen ratio is an important one, for example. Again taking the analogy with baking bread, and the inoculum of yeast, there is no recipe for this either. The digester will already be full of microorganisms and inoculum to create the reaction is not needed. But, I don’t think there are any digesters solely fed with whey, other feed materials such as manure and crop-derived material/ waste would be mixed with the whey.
I am looking for equipment for the pretreatment wheat and barley straw to use like substrate in the biodigester.
I suggest that you talk to our advertisers such as Wangen Pumps about their WANGEN BIO-MIX system, or Borger’s Powerfeed Technology
Hello Gabriel, I can offer a presentation with a team of Drycake to check your preliminary requirements and see if we have products that fit your needs. Can you email me more information at laura@drycake.com?