Corrosion Mitigation Through Biogas Desulfurization: Read on, and we will explain H2S removal from biogas, something that's also called “biogas scrubbing” in the industry.
Key Points About Biogas Desulfurization Techniques
- Hydrogen sulfide (H₂S) in biogas can cause severe corrosion to equipment, reducing system lifespan by up to 50% if left untreated.
- Physical and chemical desulfurization methods like iron oxide media and chemical scrubbing can achieve removal efficiencies exceeding 99% for varying H₂S concentrations.
- Biological desulfurization techniques offer environmentally friendly solutions with lower operational costs, though they typically require more space and careful monitoring.
- Selecting the right desulfurization method depends on six critical factors, including initial H₂S concentration, required output purity, and system scale.
- Hybrid desulfurization systems combining multiple technologies are increasingly popular for handling high H₂S loads while maximizing efficiency and reducing maintenance costs.
Why Hydrogen Sulfide Is The #1 Enemy of Your Biogas Utilization System
That rotten egg smell in your biogas isn't just unpleasant—it's a silent destroyer of equipment and efficiency. Hydrogen sulfide (H₂S) is the most problematic contaminant in biogas systems, causing rapid corrosion of metal components and poisoning catalysts in downstream equipment.
At concentrations as low as 50-100 ppm, H₂S begins attacking metal surfaces, forming metal sulfides and sulfuric acid when it combines with moisture. This corrosion can reduce the lifespan of engines, boilers, and pipelines by 30-50%, leading to frequent maintenance, expensive repairs, and frustrating system downtime.
Never forget the health hazards when considering biogas desulfurization.
“Symptoms of H2S Exposure Illustrated …” from www.pringlelaw.net and used with no modifications.
Beyond equipment damage, H₂S poses serious health and environmental risks. At concentrations above 100 ppm, it becomes a respiratory irritant, and above 1000 ppm, it can be immediately life-threatening. The removal of H₂S isn't optional—it's essential for anyone serious about harnessing biogas as a renewable energy source.
H₂S concentrations vary widely depending on feedstock type. Animal manure and food waste digesters typically produce biogas with 1,000-10,000 ppm H₂S, while wastewater treatment plants might see 100-1,000 ppm. These variations make selecting the right desulfurization approach critical to successful biogas utilization. Let's explore the most effective techniques available today.
Physical and Chemical Desulfurization Methods That Work
Physical and chemical methods represent the traditional approach to biogas cleaning, offering reliable performance across various scales. These techniques rely on chemical reactions or physical properties to capture and remove H₂S molecules from the gas stream. The right choice depends largely on your specific H₂S concentration, system size, and purification requirements.
Iron Oxide/Hydroxide Media: The Tried-and-True Solution
Iron oxide media (often called “iron sponge”) represents one of the most established and reliable desulfurization methods in the industry. This approach uses iron oxide or iron hydroxide-impregnated media—typically supported on wood chips, ceramic pellets, or specialized engineered carriers—to react with hydrogen sulfide through a simple chemical reaction. When H₂S passes through the media, it reacts to form iron sulfide while effectively removing the sulfur from the biogas stream.
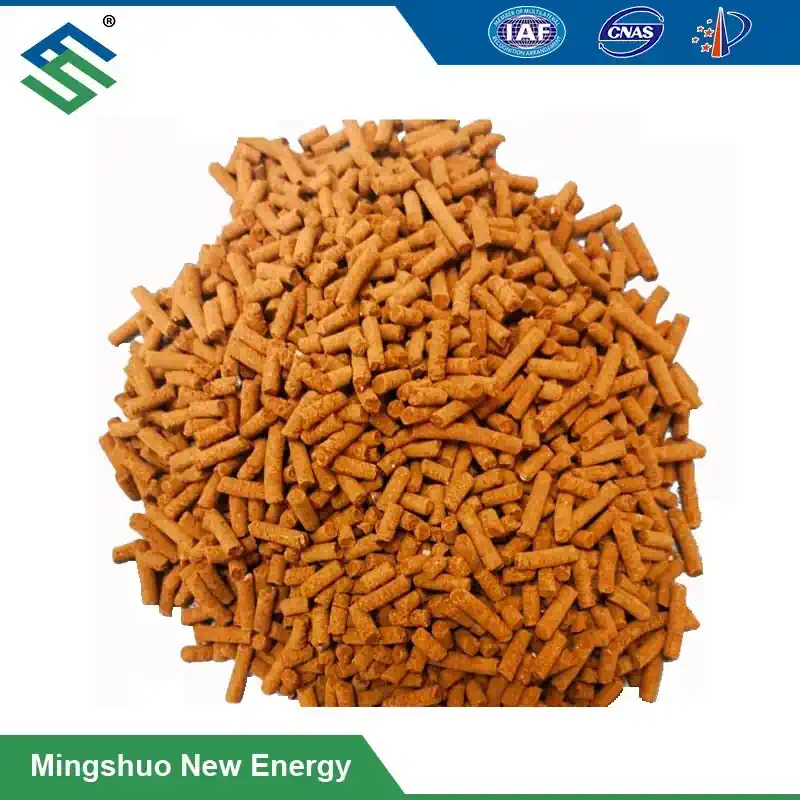
“Iron Oxide Iron Hydroxide H2s Adsorbent …” from mingshuo.en.made-in-china.com and used with no modifications.
The beauty of iron oxide systems lies in their simplicity and effectiveness. They require no electricity, operate at ambient temperatures, and can achieve removal efficiencies exceeding 99.9% when properly sized. A well-designed iron oxide system can reduce H₂S concentrations from thousands of ppm down to less than 1 ppm, making it suitable for even the most sensitive downstream applications. The media can handle H₂S concentrations ranging from a few hundred to several thousand ppm, making it versatile for various biogas sources.
However, the media eventually becomes saturated and requires replacement—typically after absorbing 25-30% of its weight in sulfur. In some cases, spent media can be regenerated through controlled exposure to oxygen, though this process is only partially effective and creates heat that must be managed carefully. For larger systems, media replacement can become labour-intensive and creates the challenge of disposing of spent material, which may be classified as hazardous waste in some jurisdictions.
Activated Carbon Adsorption for Low H₂S Concentrations
For biogas streams with lower H₂S concentrations (typically below 500 ppm) or as a polishing step after primary treatment, activated carbon adsorption offers excellent performance. Standard activated carbon works through physical adsorption, while impregnated varieties (containing potassium iodide, sodium hydroxide, or potassium hydroxide) combine physical and chemical mechanisms to boost capacity. The impregnation enhances the carbon's ability to capture H₂S, significantly increasing removal efficiency compared to standard activated carbon.
“Activated carbon » Rayeneh Group” from rayeneh.com and used with no modifications.
The main advantages of activated carbon systems include their compact footprint, simple operation, and ability to achieve very low outlet H₂S concentrations—often below 1 ppm. This makes them ideal for applications requiring extremely clean biogas, such as fuel cells or gas grid injection. The pressure drop across properly designed carbon vessels remains minimal, reducing parasitic energy losses in your biogas system.
The primary drawback is cost—impregnated activated carbon commands premium prices compared to iron oxide media, making it less economical for high-H₂S applications where large volumes would be required. Additionally, unlike iron oxide media, activated carbon typically cannot be regenerated effectively on-site, requiring complete replacement when saturated. For systems with variable H₂S loads, activated carbon often works best as a secondary treatment after a more economical primary removal stage. For more information on biogas purification methods, you can explore biogas purification techniques.
Chemical Scrubbing With Caustic Solutions
Chemical scrubbing represents a more sophisticated approach, particularly well-suited for larger biogas installations with high H₂S concentrations. This process involves passing biogas through a scrubbing tower where it contacts an alkaline solution—typically sodium hydroxide (NaOH), potassium hydroxide (KOH), or sodium carbonate (Na₂CO₃). The H₂S dissolves into the liquid and undergoes a chemical reaction that binds the sulfur in solution. For more detailed information on biogas purification techniques, you can explore biogas purification methods.
“Troubleshooting a Caustic Scrubber for biogas desulfurization| AIChE” from www.aiche.org and used with no modifications.
Water Scrubbing: Simple But Less Efficient
Water scrubbing leverages the basic principle that H₂S has greater solubility in water than methane. In this system, biogas flows counter-currently through a packed column where water cascades downward, absorbing H₂S along with CO₂. While appealingly simple in concept, water scrubbing typically achieves only moderate H₂S removal efficiency—usually 60-80% in a single pass—unless operated under pressure with significant water flow rates. For more information on desulfurization techniques, you can explore the desulfurization of biogas methods.
The main advantages of water scrubbing include low chemical costs (using only water as the scrubbing medium) and minimal environmental concerns with the process itself. For operations where water is plentiful and H₂S requirements aren't stringent, this approach offers a straightforward solution. However, the water exiting the scrubber becomes contaminated with dissolved sulfides and must be properly treated before discharge or reuse, often requiring aeration or chemical treatment.
Most modern water scrubbing systems are actually designed primarily for CO₂ removal rather than H₂S removal, making them more suitable as part of a comprehensive biogas upgrading process rather than dedicated desulfurization. For plants focused specifically on H₂S removal, other techniques typically offer better efficiency and lower operating costs.
“Wet scrubber for Biogas Desulfurization – Energy Education” from energyeducation.ca and used with no modifications.
Membrane Separation Technology
Membrane technology represents the cutting edge of physical gas separation methods. These systems use specialized polymer membranes with different permeation rates for various gas molecules. The H₂S molecules pass through the membrane more readily than methane, allowing for effective separation. Modern membranes can achieve impressive H₂S removal rates while minimizing methane loss, though they typically require pre-treatment to remove particulates and other contaminants that could damage the delicate membrane structure.
The principal advantages of membrane systems include their compact footprint, lack of moving parts, and continuous operation capability.
They're particularly valuable in space-constrained installations or where chemical use needs to be minimized. However, the technology comes with significant upfront costs and typically requires operating at elevated pressures, increasing energy consumption. Membranes also have finite lifespans and eventually require replacement, creating an ongoing operational expense.
“Hydrogen sulfide removal from natural …” from pubs.rsc.org and used with no modifications.
Biological Desulfurization: Nature's Way to Clean Biogas
Biological desulfurization harnesses nature's own sulfur-processing mechanisms to clean biogas efficiently and sustainably. These methods use specialized microorganisms that oxidize H₂S to elemental sulfur or sulfate, effectively removing it from the gas stream. Biological approaches typically offer lower operating costs than chemical methods once established, though they require more careful monitoring and control of environmental conditions. For more insights into the purification of biogas, explore our detailed guide.
In-Situ Biological Desulfurization
The simplest biological approach occurs directly inside the digester itself through micro-aeration. By carefully introducing small amounts of oxygen (typically 2-6% of the biogas volume) into the headspace or upper portion of the digester, sulfide-oxidizing bacteria naturally present in the system convert H₂S to elemental sulfur. This approach requires no additional vessels or equipment beyond an air injection system and can reduce H₂S concentrations by 80-95% under optimal conditions.
The primary advantage of in-situ desulfurization is its low cost and simplicity. It requires minimal additional equipment and uses naturally occurring bacteria already present in the digestion system. The method works particularly well for digesters with moderate H₂S levels (below 2,000 ppm) and stable operation. However, the process demands careful oxygen control—too little oxygen results in incomplete H₂S removal, while too much can inhibit the anaerobic digestion process or create potentially explosive conditions.
The elemental sulfur produced eventually settles in the digester, potentially creating maintenance challenges over time as it accumulates. Additionally, in-situ methods rarely achieve the ultra-low H₂S levels required for sensitive applications like fuel cells or pipeline injection, often necessitating a secondary cleaning step.
Biotrickling Filters: The Sweet Spot of Efficiency and Cost
Biotrickling filters represent the most widely adopted biological method for external biogas desulfurization. These systems consist of a packed column where a specialized microbial community grows on the packing material. A nutrient solution trickles down through the packing, providing essential minerals and maintaining optimal moisture for the microorganisms. As biogas flows upward through the column, sulfide-oxidizing bacteria convert H₂S to elemental sulfur or sulfate, which washes out with the trickling liquid. To understand the broader impact, explore the role of biogas in methane emissions reduction.
Modern biotrickling filters can achieve remarkable removal efficiencies exceeding 99% even with inlet H₂S concentrations above 10,000 ppm. Studies with Paracoccus pantotrophus and other specialized bacteria show consistent performance even under variable operating conditions. The process operates at ambient temperature and pressure, requiring minimal energy input beyond circulation pumps and a small air injection system to provide oxygen for the biological reactions.
“H2S in biogas using biotrickling filter …” from www.sciencedirect.com and used with no modifications.
Case Study: Danish Biogas Plant Performance
A full-scale biotrickling filter at a swine manure digester in Denmark demonstrated consistent H₂S removal from 2,000-5,000 ppm down to below 50 ppm, with efficiency exceeding 99% during its two-year operational period. The system handled flow rate variations from 50-150 m³/hour without performance degradation while requiring only minimal maintenance and nutrient addition.
Bioscrubbers for High-Volume Applications
Bioscrubbers separate the absorption and biological oxidation processes into two distinct stages. First, H₂S absorbs into a liquid medium in a scrubbing column. Then, this sulfide-rich liquid enters a separate bioreactor where specialized microorganisms convert the dissolved sulfides to elemental sulfur or sulfate. The cleaned liquid recirculates back to the absorption column, creating a continuous process loop. This two-stage approach offers precise control over each process but requires more complex equipment and monitoring.
The advantage of bioscrubbers lies in their ability to handle very high gas flow rates and fluctuating H₂S concentrations. By separating the absorption and biological processes, each can be optimized independently. The liquid buffer between stages helps smooth out variations in the incoming H₂S load, providing more consistent performance. However, bioscrubbers typically have higher capital costs and complexity compared to biotrickling filters, making them better suited to larger installations where their superior control capabilities justify the additional expense.
Biofilters: Low-Cost But Space-Intensive
Traditional biofilters use natural organic materials like compost, wood chips, or soil as both the support medium and initial inoculum for sulfide-oxidizing bacteria. Biogas passes through this moist organic bed where microorganisms convert H₂S to elemental sulfur and sulfate. While technologically simple, biofilters typically require large surface areas and careful moisture management to maintain efficiency. They work best for lower gas flow rates and moderate H₂S concentrations, making them suitable for smaller biogas installations.
The primary advantages of biofilters include their low capital cost, simple construction, and minimal chemical requirements. They can be built using locally available materials and require relatively simple maintenance procedures. However, traditional biofilters struggle with high H₂S concentrations, have larger footprints than other biological methods, and can experience channeling or compaction issues over time. Modern variations using synthetic media and improved irrigation systems address some of these limitations, though typically at higher cost.
6 Factors to Consider When Choosing a Biogas Desulfurization Method
Factor | Key Consideration | Best Methods for Different Scenarios |
---|---|---|
H₂S Concentration | Low (0-500 ppm), Medium (500-3,000 ppm), High (>3,000 ppm) | Low: Activated carbon, In-situ Medium: Iron oxide, Biotrickling High: Chemical scrubbing, Two-stage biological |
Required Purity | Boiler (≤1,000 ppm), Engine (≤500 ppm), Pipeline (≤4 ppm) | Low requirements: In-situ, Biofilters High requirements: Chemical scrubbing, Activated carbon |
System Scale | Small (<100 m³/h), Medium (100-500 m³/h), Large (>500 m³/h) | Small: Iron oxide, In-situ Medium: Biotrickling filters Large: Chemical scrubbing, Bioscrubbers |
Operating Costs | Media replacement, Chemical consumption, Energy use | Lowest: In-situ biological Highest: Chemical scrubbing, Activated carbon |
Environmental Impact | Chemical use, Waste products, Resource consumption | Lowest: Biological methods Highest: Chemical scrubbing with non-regenerable solutions |
Integration | Space requirements, Complexity, Monitoring needs | Simplest: In-situ, Iron oxide vessels Most complex: Membrane systems, Chemical scrubbers |
Selecting the right desulfurization approach requires careful analysis of your specific situation and requirements. The six factors above form a framework for making this critical decision. An undersized or inappropriate system can lead to inadequate H₂S removal and equipment damage, while oversized systems waste capital and operating resources. Taking time to properly assess your needs now will pay dividends throughout your biogas system's operational life.
No single desulfurization technology works optimally for all situations. The biogas industry has moved away from one-size-fits-all approaches toward customized solutions that match specific site conditions, operational requirements, and economic constraints. Many modern installations employ combination approaches to maximize efficiency while minimizing costs. For instance, the development of biogas for electricity highlights the importance of tailored solutions in addressing technology challenges.
Hybrid Systems: Combining Methods for Maximum Results
The biogas industry is increasingly adopting hybrid desulfurization approaches that combine complementary technologies to address limitations of single-method systems. These integrated solutions leverage the strengths of different processes to handle varying H₂S loads more efficiently while minimizing operational challenges. For instance, a biotrickling filter followed by an activated carbon polishing stage provides robust removal during normal operation with added protection during peak H₂S events.
Two-Stage Systems for High H₂S Loads
Two-stage desulfurization systems have proven particularly effective for biogas with high or variable H₂S concentrations. A common configuration pairs a chemical or biological primary treatment stage with a polishing step using activated carbon or iron oxide media. This arrangement allows the first stage to handle the bulk of the H₂S load (often removing 90-95%), while the second stage captures the remaining contaminants to achieve ultra-low outlet concentrations. The primary benefit is extended media life in the polishing stage, as it encounters only a fraction of the total H₂S load.
Another promising hybrid approach combines biological oxidation with chemical processes. Research has demonstrated exceptional performance from systems using nitrate reduction coupled with H₂S oxidation in two-stage bioreactors. These systems achieve reliable performance even with inlet H₂S concentrations above 10,000 ppm while producing minimal waste streams. The microorganisms use nitrate rather than oxygen as the electron acceptor, eliminating oxygen contamination concerns in the treated biogas.
Pre-Treatment Options to Extend Media Life
Strategic pre-treatment can dramatically improve the economics of downstream desulfurization processes. For digesters with particularly sulfur-rich feedstocks, adding iron chloride or ferric sulfate directly to the digester can precipitate sulfides before they convert to H₂S. This approach can reduce H₂S production by 60-80%, significantly extending the life of external desulfurization media and reducing overall operating costs despite the additional chemical expense.
Innovative pre-conditioning techniques like controlled micro-aeration in a separate vessel before the main desulfurization stage have shown promising results in recent field trials. This pre-treatment initiates biological oxidation processes that reduce the load on downstream systems while avoiding the risk of oxygen contamination in the digester itself. When combined with main-stage desulfurization, these approaches create robust, multi-barrier systems capable of handling wide variations in H₂S concentrations reliably.
Real-World Application: Which Method Works Best for Different Scenarios
The theoretical capabilities of desulfurization technologies only tell part of the story. Real-world applications demonstrate which approaches truly deliver under various operational conditions. Let's examine how different biogas operations typically approach their desulfurization needs based on practical considerations and field experience.
Small Farm Digesters (Under 100 m³/hour)
Small agricultural biogas plants typically prioritize simplicity, low maintenance requirements, and minimal capital investment. For these installations, in-situ biological desulfurization often provides the most practical first-line approach, requiring only a small air injection system and basic monitoring equipment. When combined with a simple iron oxide media vessel for polishing, this approach delivers reliable performance with minimal operator intervention. The iron media typically requires replacement only 2-4 times per year depending on H₂S loads, making maintenance manageable even with limited staff.
Industrial-Scale Biogas Plants
Large industrial biogas facilities processing food waste, agricultural residues, or industrial byproducts typically generate biogas with both high flow rates and elevated H₂S concentrations. These operations generally benefit from biotrickling filters or chemical scrubbing systems that can handle high-volume throughput with consistent performance. The economics often favour biological systems due to lower operating costs, though chemical approaches may be preferred where space is limited or extremely consistent performance is required regardless of temperature variations or other environmental factors.
Landfill Gas Collection Systems
Landfill gas presents unique challenges with its variable composition, fluctuating flow rates, and presence of siloxanes and other contaminants alongside H₂S. Most modern landfill gas operations employ multi-stage treatment trains with specialized media beds targeting different contaminants. For H₂S specifically, regenerable iron-based media systems have proven particularly effective, offering good removal efficiency while minimizing media replacement frequency through in-place regeneration capabilities.
The relatively low but still problematic H₂S concentrations in landfill gas (typically 50-300 ppm) make activated carbon an attractive option, especially impregnated varieties designed specifically for simultaneous removal of H₂S and siloxanes. While more expensive per unit volume than iron oxide media, the dual-contaminant removal capability often justifies the premium for landfill applications.
Installation and Maintenance Best Practices
Even the most advanced desulfurization technology will underperform without proper installation and maintenance. System design should incorporate sufficient flexibility to handle variations in gas composition and flow rate while remaining economical. Regular monitoring and preventive maintenance significantly extend system life and maintain peak performance. Planning for eventual media replacement or regeneration from the initial design stage prevents costly retrofits later.
Proper Sizing and Redundancy Planning
- Oversize vessels by 20-30% beyond minimum requirements to handle flow and concentration spikes
- Install parallel treatment trains where feasible to allow maintenance without complete system shutdown
- Include bypass capabilities and isolation valves to facilitate media replacement or regeneration
- Design for future expansion if biogas production is expected to increase
- Install sampling ports before and after each treatment stage for performance monitoring
Proper vessel sizing represents perhaps the most critical design decision. Undersized systems lead to incomplete H₂S removal and frequent media replacement, while oversized systems waste capital and may cause channeling issues in media beds. Contact time between the biogas and the treatment media (often expressed as Empty Bed Contact Time or EBCT) must be sufficient for the desired removal efficiency. For iron oxide media, this typically ranges from 60-180 seconds depending on inlet H₂S concentration and required outlet purity. Learn more about decarbonization strategies using biogas and how they can impact design decisions.
Temperature management deserves special attention, particularly for biological systems. Most sulfide-oxidizing bacteria perform optimally between 25-35°C, with significantly reduced activity below 15°C. For installations in cold climates, insulating biotrickling filters and heating nutrient solutions may be necessary to maintain performance during winter months. Chemical and physical systems generally show less temperature sensitivity but may still benefit from insulation to prevent condensation issues.
Pressure drop across the system affects both performance and energy consumption. Well-designed systems typically maintain pressure drops below 50 mbar to minimize parasitic loads on blowers or compressors. Regular monitoring of differential pressure provides an excellent early warning of media fouling, channeling, or excessive moisture accumulation that could compromise system performance.
Documentation and training often receive insufficient attention but prove crucial for long-term success. Comprehensive operation manuals, clear maintenance schedules, and proper operator training ensure systems perform as designed throughout their operational life. Establishing clear performance benchmarks and monitoring protocols helps identify developing issues before they become critical problems. For instance, understanding the anaerobic digester farm equipment can significantly enhance operational efficiency.
H₂S Monitoring Equipment
Effective H₂S monitoring forms the foundation of successful desulfurization system management. Online continuous monitors provide real-time feedback on system performance, allowing operators to detect breakthrough before it damages downstream equipment. For smaller systems where continuous monitoring may be cost-prohibitive, regular testing with hand-held devices or colorimetric tubes offers a practical alternative. Learn more about decarbonization strategies for energy from biogas to enhance your system's efficiency.
Monitoring Biogas Desulfurization – “Hydrogen Sulfide (H2S) Gas Detector …” from www.amazon.com and used with no modifications.
Fixed-point H₂S sensors installed before and after treatment stages provide the most comprehensive performance data. Modern electrochemical sensors offer reasonable accuracy in the 0-1000 ppm range with minimal maintenance requirements. For higher concentrations, dilution systems or specialized high-range sensors may be required. Many operators now connect these monitoring systems to automated alerts that notify maintenance personnel when H₂S levels approach action thresholds. For more information on related technologies, you can explore anaerobic digester farm equipment system solutions.
Gas chromatography represents the gold standard for comprehensive biogas composition analysis
“Gas Chromatography | GeeksforGeeks” from www.geeksforgeeks.org and used with no modifications.
, though its complexity and cost make it impractical for continuous monitoring. Periodic professional lab analysis using GC methods provides valuable calibration reference points for simpler day-to-day monitoring systems and can identify trace contaminants that might affect desulfurization performance.
Personal safety monitors should always be available to operators working around biogas systems. These portable devices alert workers to dangerous H₂S concentrations and should be standard equipment for anyone entering areas where biogas leaks could potentially occur. Remember that H₂S can cause olfactory fatigue (inability to smell it) at concentrations above 100 ppm, making detection equipment essential for safety.
- Electrochemical sensors for continuous online monitoring (0-1000 ppm range)
- Colorimetric tubes for spot checks and verification
- Portable multi-gas detectors for maintenance personnel safety
- Automated data logging systems for performance tracking and trend analysis
- Alarm systems with multiple trigger points for early warning and emergency response
Safety Protocols When Handling Desulfurization Media
Spent desulfurization media can pose significant safety hazards if handled improperly. Iron sulfide, formed when iron oxide media reacts with H₂S, can spontaneously ignite when exposed to oxygen under certain conditions. This pyrophoric reaction has caused numerous fires during media replacement operations. Proper wetting procedures, controlled exposure to air, and appropriate personal protective equipment are essential when handling spent media. Always follow manufacturer guidelines and ensure all personnel understand the associated risks.
Chemical desulfurization agents present their own safety considerations. Caustic solutions can cause severe burns, while some chemical reagents may release toxic gases if mixed improperly. Dedicated chemical storage areas with appropriate containment, clear labeling, and material safety data sheets readily available help minimize these risks. All personnel should receive thorough training on emergency procedures, including spill response and first aid for chemical exposure.
The Bottom Line: Protecting Your Investment Through Effective Desulfurization
Effective H₂S removal represents one of the most crucial aspects of biogas system management. The relatively modest investment in proper desulfurization technology protects far more expensive downstream equipment while ensuring consistent energy production. When selecting and implementing a desulfurization approach, consider the entire lifecycle cost—including media replacement, maintenance requirements, and energy consumption—rather than focusing solely on initial capital investment.
The biogas industry continues to innovate in desulfurization technology, with new media formulations, more efficient biological processes, and smarter control systems emerging regularly. Staying informed about these developments can help operators optimize their desulfurization approach as systems age and potentially require upgrading. BiogasWorld's technical resources provide valuable insights into emerging technologies and best practices for biogas purification.
Expert Insight: “Most biogas system failures we investigate trace back to inadequate H₂S removal. Proper desulfurization is not where operators should economize—it's the insurance policy that protects your entire investment in biogas utilization equipment.” — Dr. Lars Jørgensen, Biogas Systems Engineer
Whether you're planning a new biogas system or optimizing an existing installation, prioritizing effective desulfurization will pay dividends through extended equipment life, reduced maintenance costs, and more consistent operation. The right approach balances initial cost, operating expenses, performance requirements, and system reliability to deliver clean, usable biogas that fulfils its promise as a renewable energy source.
Frequently Asked Questions About Biogas Desulfurization
Common Questions About Biogas Desulfurization
These questions represent the most frequently asked topics from biogas system operators regarding H₂S removal technologies and practices.
Understanding the practical aspects of desulfurization system operation helps operators make informed decisions about technology selection, maintenance scheduling, and troubleshooting. The following questions address common concerns we hear from biogas system managers across various applications and scales. For more insights, explore the role of biogas in methane emissions reduction.
Proper maintenance scheduling depends heavily on your specific system design, H₂S loading, and performance requirements. The guidelines below provide starting points, but monitoring remains the most reliable way to determine actual maintenance needs for your particular installation. For more information on purification methods, you can explore biogas purification techniques.
System design should always prioritize safe access for maintenance procedures. Confined space entry requirements, media handling logistics, and equipment accessibility all affect maintenance costs and safety. Investing in good design upfront minimizes these concerns throughout the system's operational life. For more information on system design, consider exploring BGasTech's insights on biogas systems.
Always consult equipment manufacturers for specific maintenance recommendations regarding their technologies. The general guidance below reflects industry experience but may not address unique aspects of proprietary systems or special operating conditions.
How often do I need to replace iron oxide media in a desulfurization system?
Replacement frequency for iron oxide media depends primarily on H₂S loading and vessel sizing. Properly sized systems typically require replacement when media has absorbed 25-30% of its weight in sulfur, which translates to roughly 150-300 kg of sulfur removed per cubic meter of media. In practical terms, this means replacement intervals ranging from 3-12 months for most applications. Monitoring breakthrough (when H₂S begins appearing in the outlet gas) provides the most reliable indication that replacement is needed. Many operators maintain a schedule based on historical performance but verify with regular outlet gas testing to catch early breakthrough before it damages downstream equipment.
Can desulfurization systems handle fluctuating H₂S levels?
Most desulfurization systems can accommodate moderate fluctuations in H₂S levels, though their ability to handle extreme variations differs significantly by technology. Chemical scrubbing systems typically offer the best performance under highly variable conditions, as they can rapidly adjust reagent dosing to match changing H₂S concentrations. Properly sized media-based systems provide good buffer capacity against short-term spikes but may struggle with sustained increases above design capacity.
Biological systems typically require more stable conditions, as the microbial communities need time to adapt to changing H₂S loads.
However, modern biotrickling filters with optimized control systems can handle variations of ±50% around the design concentration with minimal performance impact. For systems facing extreme variability, two-stage approaches combining different technologies often provide the most reliable performance across the entire operating range.
What's the minimum H₂S level that requires treatment?
The threshold for H₂S treatment depends entirely on your downstream equipment and biogas utilization pathway. For boilers, H₂S levels below 1,000 ppm typically cause only gradual corrosion, though even these concentrations will eventually damage equipment and may violate emission regulations.
Engine manufacturers generally specify maximum H₂S tolerances between 100-500 ppm, though engine life will be maximized at lower concentrations. For pipeline injection or vehicle fuel applications, extremely stringent requirements apply—often below 4 ppm for pipeline and below 10 ppm for compressed natural gas vehicle fuel. Fuel cells and catalytic processes typically require near-complete H₂S removal, with maximum allowable concentrations below 1 ppm to prevent catalyst poisoning.
Are biological desulfurization systems affected by cold temperatures?
Temperature significantly impacts biological desulfurization performance. Most sulfide-oxidizing bacteria exhibit optimal activity between 25-35°C (77-95°F), with performance declining as temperatures drop below 15°C (59°F). In cold climates, biotrickling filters and bioscrubbers typically require insulation and possibly heating systems to maintain reliable year-round operation. The nutrient solution in biotrickling filters provides an excellent heat transfer medium, and simple heat exchangers can maintain suitable temperatures even in sub-freezing ambient conditions.
Some specialized bacterial strains show better cold tolerance, with reasonable activity down to 10°C (50°F). Research into psychrophilic (cold-loving) sulfide oxidizers continues, but commercial systems generally rely on temperature management rather than specialized bacteria. For locations with severe winters, hybrid systems incorporating chemical or physical methods as backup during extreme cold spells offer the most reliable approach.
How do I dispose of spent biogas desulfurization media properly?
- Determine regulatory classification: Spent media may be classified as non-hazardous or hazardous waste depending on composition and local regulations
- Analyze for leachable sulfides and heavy metals that may affect disposal options
- Consider potential for regeneration or beneficial reuse before disposal
- Document chain of custody and obtain disposal certificates for compliance records
- Follow manufacturer recommendations for handling and transportation safety
Proper disposal practices vary by media type and local regulations. Spent iron oxide media often contains elemental sulfur and iron sulfide compounds that may be classified as hazardous in some jurisdictions due to potential reactivity and leachability concerns. Some manufacturers offer take-back programs for spent media, either for proper disposal or regeneration. Agricultural applications sometimes permit land application of certain spent biological media as soil amendments, though this requires regulatory approval based on composition analysis. For more information on biogas applications, explore biogas for electricity and its technology challenges.
For activated carbon and specialized media, thermal regeneration facilities can sometimes restore adsorptive capacity, though transportation costs to these facilities must be considered. Regardless of the chosen disposal pathway, proper documentation remains essential for regulatory compliance. Work with qualified waste management professionals familiar with local requirements to ensure appropriate handling and disposal. For a deeper understanding of the technology challenges, you can explore biogas for electricity as a renewable power source.
Remember that spent media from biological systems may contain valuable nutrients and organic matter that could be beneficially reused. Recent research demonstrates potential for composting certain biological desulfurization byproducts or incorporating them into soil amendment products. These circular economy approaches can transform a waste disposal challenge into a valuable resource while reducing overall environmental impact.
Careful planning for media disposal should begin before system installation, as disposal costs can significantly impact lifecycle economics. Some technologies with higher upfront costs may prove more economical over time if they produce less waste requiring special handling. BiogasWorld's comprehensive biogas upgrading solutions include end-of-life considerations for all system components, ensuring environmental responsibility throughout the equipment lifecycle.
Biogas desulfurization is a crucial step in ensuring the longevity and efficiency of biogas systems. The presence of hydrogen sulfide in biogas can lead to severe corrosion of equipment and infrastructure. Various techniques have been developed to address this issue, including chemical absorption and biological filtration. For a deeper understanding of these techniques, you can explore the biogas purification methods that are currently being researched and implemented.