A new sustainable NPK fertiliser technology has been patented (using digestate) which makes a conventional NPK mineral fertiliser replacement tailored for customer's fields. Not only does this technology utilise digestate fibre, but it also uses the carbon dioxide captured, either:
- during biogas upgrading to pure biomethane, or
- from the biogas engines used to generate electricity.
Finally, the icing on the cake will be the “cloud app” capable of providing tailor-made pellets or granulation formulations for every batch to the buyer's field data and crop requirements.
The new process, developed by CCm Technologies, Swindon, UK, uses captured carbon dioxide to stabilise, nitrogen, phosphate and organic chemicals held within waste streams, turning them into sustainable plant nutrients.
The proprietary green nitrogen fertilizer process may sound too good to be true. Yet this article was compiled from available press releases and the content of a recent presentation by CCm Technologies to the ADBA Northern Ireland Conference in September 2021 and subsequently updated.
Why Sustainable NPK Fertiliser Matters
Agriculture is the backbone of our global food supply, but it has long relied on mineral-based fertilisers derived from non-renewable resources. These conventional fertilisers, while effective, pose significant environmental challenges, including soil degradation, water pollution, and greenhouse gas emissions. Our sustainable NPK fertiliser technology addresses these issues by harnessing the power of digestate—a nutrient-rich byproduct of anaerobic digestion.
The Environmental Impact of Traditional Fertilisers
Traditional NPK fertilisers are composed of nitrogen (N), phosphorus (P), and potassium (K), essential nutrients for plant growth. However, their production is energy-intensive and relies heavily on finite resources such as natural gas and phosphate rock. The environmental footprint of these fertilisers includes:
- Greenhouse Gas Emissions: Manufacturing processes release significant amounts of CO₂ and other greenhouse gases.
- Resource Depletion: Dependence on non-renewable resources threatens long-term agricultural sustainability.
- Water Pollution: Runoff from fertiliser application can contaminate water bodies, leading to eutrophication and harm to aquatic ecosystems.
By transitioning to digestate-based NPK fertilisers, we can mitigate these impacts and promote a more sustainable agricultural framework.
What is Digestate?
Digestate is the residual material left after the anaerobic digestion of organic matter, such as agricultural waste, food waste, and livestock manure. This process not only produces renewable energy in the form of biogas but also results in a nutrient-rich substance ideal for fertilising crops.
Benefits of Using Digestate
- Nutrient-Rich: High concentrations of nitrogen, phosphorus, and potassium make digestate an effective fertiliser.
- Renewable Resource: Produced from organic waste, reducing reliance on non-renewable mineral sources.
- Soil Health: Enhances soil structure, water retention, and microbial activity, promoting long-term fertility.
- Waste Management: Provides a sustainable solution for managing agricultural and organic waste streams.
Sustainable NPK Fertiliser Process is Destined to Significantly Reduce Greenhouse Gas Emissions
This stabilisation process significantly reduces greenhouse gas emissions on-site and the carbon-free heat co-generated by CCm’s proprietary process combines with recovered heat to reduce energy consumption across the site. This in turn will further assist:
- agricultural and industrial anaerobic digestion (biogas) plant operators, and
- water utilities, in their drive toward Zero Carbon operations.
The process will use the existing output material (“resources”) available at a variety of waste treatment facility types. However, it appears to have the largest synergy when applied at those increasingly common biogas plants which further process their raw biogas to high purity biomethane.
Until now the high ammonia present in the digestate from anaerobic digestion has been a concern. At best digestate requires careful handling to:
- avoid exceeding permissible soil ammonia levels when applied to land
- prevent the emission of ammonia to the atmosphere (NOx emissions).
pH adjustment is required at the very least. However, an ammonia input is also, not unexpectedly, a requirement for this process. Hence, available ammonia is needed
The bottom line is that CCm’s proprietary process is seen as significantly reducing both:
- the cost and
- the carbon footprint of fertiliser,
by drawing most of the ingredients from current waste sources.
CCm’s Proprietary Sustainable NPK Fertiliser Will Comply with the Waste Hierarchy and Help Drive the Circular Economy
“The opportunity to use the carbon dioxide on the land and create new life really is the waste hierarchy and circular economy put into best practice.”
CCm’s Chief Technology Officer, Professor Peter Hammond, explained:
“The process begins with a cellulosic material – such as grass, agricultural and food waste, wood chip, partially composted materials or, in this case, digestate from the AD plant.
“Coating the material with a nitrogenous material allows carbon dioxide to be attached and stabilised to create a strong carbonate material. Additional plant nutrient material, most likely recycled, can be added to tailor the final fertiliser formulation prior to pelletisation or granulation.”
What “NPK Fertiliser” Means
The three numbers generally published on fertiliser product packages represent the value of the three macro-nutrients used by plants.
These macro-nutrients are nitrogen (N), phosphorus (P) and potassium (K), or NPK for short. The higher the number, the more concentrated the nutrient is in the fertiliser.
Nitrogen is largely responsible for the growth of leaves on the plant, phosphorus is largely responsible for root growth and flower and fruit development and potassium is a nutrient that helps the overall functions of the plant perform correctly.
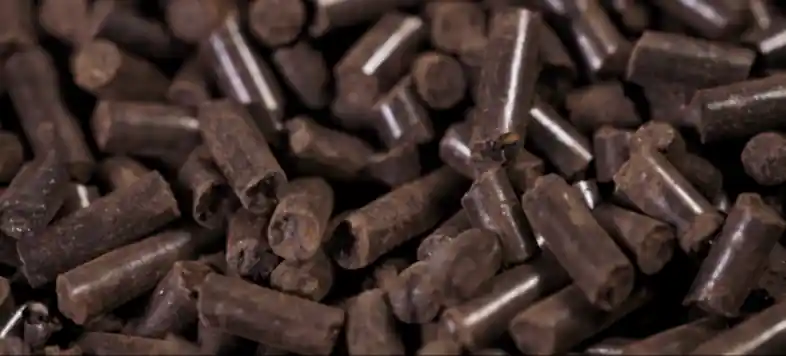
“CCm Technologies – Carbon Capture and …” from www.ccmtechnologies.co.uk and used with no modifications.
Case Study of CCm’s Proprietary Fertiliser Production Process in Use So Far
Four case studies are described to date on the CCm website of which the most advanced is:
- A Water Utility Company Wastewater Treatment Facility (Sewage Works) operated by Severn Trent Water (Minworth WWTF).
CCm's Sustainable – NPK Fertiliser Severn Trent Water Collaboration at Minworth WWTF
The collaboration with CCm Technologies, an award-winning cleantech company focused on
resource optimisation. The aim was to develop an enhanced fertiliser product for agricultural and/or horticultural application, potentially creating new commercial opportunities for Severn Trent. A full-scale CCm unit has been commissioned at the UK’s 3rd largest sewage treatment works serving the Birmingham area and is currently completing its optimisation phases successfully delivering various different fertiliser formulations at volume.
Application extensions have been developed for the sewage sector allowing for the capture of the waste Phosphorous and Ammonia, currently being discharged into watercourses, to be integrated with CCm’s upgrading of the bio-solids into fertiliser.
Professor Hammond said the technology has the potential to directly save or avoid the production of millions of tonnes of carbon dioxide and could demonstrate the
“importance’ of carbon capture and utilisation, as opposed to storage, in reducing global greenhouse gases.”
The project has been supported by the Department for Business, Energy and Industrial Strategy (BEIS) and Innovate UK. The purpose was to demonstrate the commercial potential for the technology in resolving some of the climate change challenges faced by the water utility sector.
Who are “CCm Technologies”?
CCm Technologies is a sustainable/cleantech technology company, based in Swindon, UK.
They are focused on resource optimisation, including Carbon Capture and Utilisation (CCU). CCm's technology converts captured CO2 and other waste streams (such as Ammonia and Phosphate) into stable value-added materials with multiple uses across global priority sectors of food/agriculture, advanced materials and energy storage.
The significantly exothermic patented process is based on high primary capture efficiencies from novel cellulose/amine capture material which retain 95% of flue-sourced CO2. Heat storage is a separate application of the technology that stores thermal energy with a chemical reaction and following release can, like a battery, be recharged.
A Key Challenge for the AD Process Solved by CCm
One of the key challenges of anaerobic digestion is how to deal with the byproducts, including the CO2 produced, in a sustainable and cost-effective way.
The full-scale commercial unit that's deployed at Severn Trent's Minworth facility is located at the third largest sewage farm in the UK. It has gone through commissioning and optimization and has a boilerplate output at the back end of 10,000 tons of fertiliser per annum.
CCm needs four things to make fertiliser:
- Organic Fibre: Depending on the sector that they are working with it's either a biosolid sludge, a digestate cake, or a straw or any other type of waste fibre.
- A Biogenic or Recovered Ammonia source
- Phosphorus and
- CO2
and optionally, if there is some waste heat anywhere on a site they are always grateful for that.
The outcome is twofold, one is a high-grade fertiliser that comes in pellet form but can come in granules that are customizable so we're not saying that this week's inputs are A, B, C and therefore the only fertiliser we can produce is is “Z”.
This is about producing exactly what a farmer wants and because the process is exothermic we are also in a position to provide the operator with some zero-carbon thermal energy as well.
Every system will be on full automation and control weigh-scales, sensors, monitors, and make the product. Once done, all of the data will be held on their proprietary platform on the Microsoft Azure Cloud.
This they see as critical for a number of reasons:
- The operator will want full transparency on what's in his fertiliser batch
- Regulators are going to become more and more desiring of the data trail. This will provide a data trail on any unit deployed at any point in time. it will also be accessible wherever they are.
- The data will be needed to quantify and gain verification for carbon offsets. They are working with Microsoft to ensure that information becomes available.
Additional CCm Fertiliser Projects in Progress
Agricultural slurries are another possible source for the CCm sustainable NPK fertiliser process. So, they are involved in a project in which they will take cattle slurry into an all-waste AD system.
The primary input will be cattle slurries supplemented by chicken waste.
The waste from the local facilities of three large food manufacturing companies will be used to supplement the animal slurries.
3 anaerobic digesters with their biogas output going into transportation as green fuel in the form of compressed renewable natural gas. Meanwhile, CCm will be dealing with the digestate cake and decarbonizing the whole project on food waste.
Pepsico is their largest contract as announced in December 2020. They will handle the potato waste from the production of crisps. Pepsico owns the Walkers brand amongst others.
By turning potatoes waste into a specific fertiliser tailored specially to the optimum NPK ratio for supplying their farming fertiliser chain, will enable their suppliers to grow more potatoes on a net-zero basis.
That would mean Pepsico's marketing would be able to point out that their potatoes will be grown with a carbon footprint easily 70% less than in the last couple of years.
What they are doing for wastewater and food waste processing is:
- transforming biosolid sludge wastes into quality-controlled compound fertilisers
- extracting those resources from available ammonia
- providing a valuable use for carbon dioxide extracted from biogas
- reducing discharges of phosphorus into groundwater and rivers.
Once again with phosphorus, they are tackling one of the really big challenges for water treatment. But the problem of volatilization of ammonia will possibly be the biggest attraction for agriculture.
Water utilities will likely focus on phosphorus extraction to prevent build-up in groundwater, and eutrophication of rivers and seas. On that, they are working with Yorkshire Water.
Finally, they have received a contract from the UK government to utilise biochar. It is a very useful fibrous material for CCm.
Look out for them showcasing their technology as it relates to biochar at COP26.
The CCm process is broadly carbon neutral compared to a Haber-Bosch process manufactured artificial fertiliser and they are simultaneously sequestering carbon into the soil.
So, they are talking about removing 1.7 million tonnes of CO2 equivalent per annum. Using the United Airlines metric that they explain that everybody is starting to use. Applying that liberally, that's the equivalent of taking over 370 000 cars off the road every year.
Conclusion
CCm has developed a revolutionary new process for sustainable NPK fertiliser production which has an amazing number of synergistic advantages.
CCm hopes to develop with their partners, specific fertiliser formulations to meet the needs of different plants and varying growing conditions on farms and in horticulture that are competitive with the nutrient inputs and price of conventional fertiliser.
The plan is to continue developing an integrated, sustainable system that maximizes the efficacy of the waste that is being transformed into renewable organic fertiliser.
If CCm Technologies accomplish even a portion of their aims their technology will have a big impact in achieving global Net-Zero targets.
Frequently Asked Questions
What is the difference between traditional and digestate-based fertilisers?
Traditional fertilisers are typically mineral-based and derived from non-renewable resources, whereas digestate-based fertilisers are produced from organic waste through anaerobic digestion. This makes them more sustainable and environmentally friendly.
How is digestate processed into NPK “Green” fertiliser?
Digestate undergoes advanced processing to extract and concentrate essential nutrients like nitrogen, phosphorus, and potassium. This ensures a consistent and effective fertiliser product tailored to specific agricultural needs.
Are there any additional costs associated with switching to digestate-based fertiliser?
While initial setup costs may vary, the long-term benefits, including reduced input costs and potential access to incentives, often result in overall cost savings.
Can digestate-based fertiliser be used for all types of crops?
Yes, CCm custom formulations can be tailored to suit a wide range of crops, ensuring optimal nutrient delivery for various agricultural applications.
Join the Sustainable Agriculture Movement
Embracing sustainable fertiliser solutions is not just a trend—it's a necessary step towards ensuring food security and environmental health for future generations. Our sustainable NPK fertiliser technology, powered by digestate, offers a viable and effective alternative to traditional non-renewable options.
Take the Next Step
Ready to transform your farming practices and contribute to a sustainable future? Contact CCm Technologies today to learn more about our custom fertiliser solutions and how they can support your agricultural goals.
[First published 21 October 2021. Updated 12 May 2025.]
A sufficient supply of nutrients is critical for crop health and yield. Mineral fertilisers play a critical role in achieving the yield and returns that farmers expect and that a growing global population requires.